TELL TALES: LISTEN TO YOUR CLIENT
22 February 2022
In my previous blog I covered mainly our serial production models and the reason/reasons why we, during later years, moved over to large custom projects. As I mentioned, the main reason, was the cost increase and the fact that serial production yards had changed to a very industrial type of production, producing a huge number of yachts in a very organized way, enabling them to cut cost hence the price difference compared to “our way of building yachts” increased to the point that we lost market shares and were forced to adapt and change.
We had neither the possibility nor the desire to go into the extreme serial production, it would have required a huge investment and more important we would have needed to go away from some of our philosophy, quality, and technology standards and in addition reduce the project customization we traditionally had offered.
Like earlier stated we had, in reality, no other alternative than moving into the large yacht custom segment where our philosophy, knowledge and capabilities were more suitable.
There are also some advantages with working with custom projects. We did have higher flexibility, in our serial models, than most of our competitors. We did some custom interior layouts, special keels, both racing and shallow draft types etc. etc. However, when you start from an existing hull there are limitations on how far you can go without compromising performance and handling characteristics. The hull volumes were design for a given displacement and if you added too much weight, at some point, your modifications would affect performance and handling to a point that your sailing characteristics might not be optimum. The same problem also exists for clients that wanted to go extreme racing. You can build a yacht lighter by going extreme in construction but if you start from a given hull shape it might not be the optimum solution. You could have had a hull with less underwater volume hence straighter and more easily driven lines and shapes. So, with the standard models we could optimize the specifications, layouts and construction in order to suite the individual owners’ priorities and requests but only to a certain point.
Another very positive side of the custom project type of production is that you are given the possibilities to work on a much broader contact basis with trade people and especially Designers. Looking back at our custom activities I can state that we have had the great fortune and pleasure to create super projects with, not only, some very interesting clients but also together with some of the world’s most successful and knowledgeable Naval Architects. This has, needless to say, increased our knowledge base in a way that likely would not have been the case if we had stuck, mainly, to standard models.
Baltic Yachts have, until today, produced 55-60 custom projects with some being produced and developed at this moment.
During these years we have worked with a good number of Naval Architects, with projects, as per following statistics.
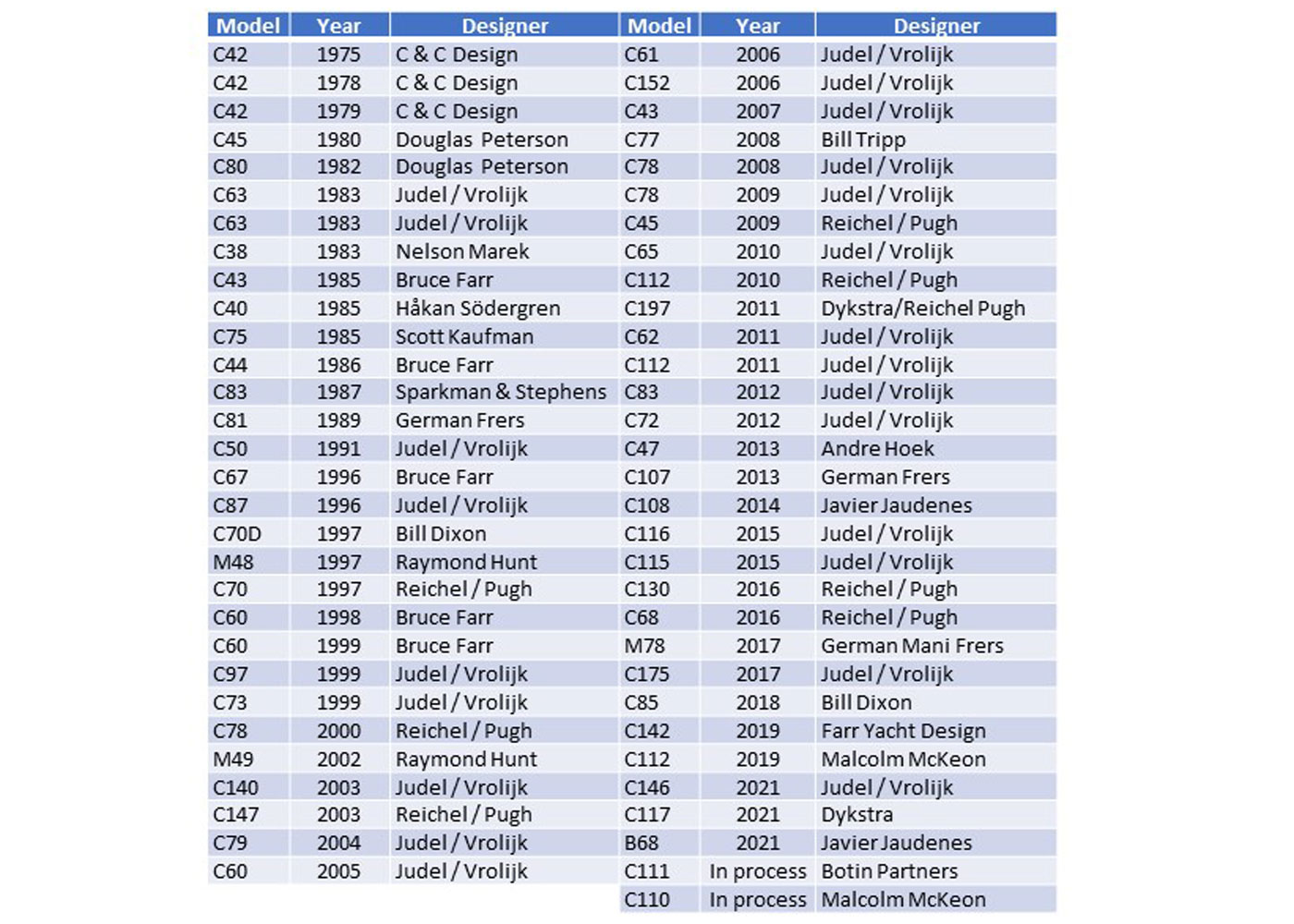
As can be seen from the above, the number of yachts is substantially less than our serial production models. However, in turnover they represent a much higher number. They also represent a wider range of philosophy when it comes to Racing – cruising and concept, some very extreme racing and performance yachts but also some very cruising minded projects.
In this media it is naturally not possible to go through all of these projects in detail but perhaps a few of them should be mentioned. Looking at it from a historical point of view I can mention that the first three on this list, C&C Designed 42 footers were based on the Baltic 42 lines but with almost no interior just the basic and for the rest pipe berths.
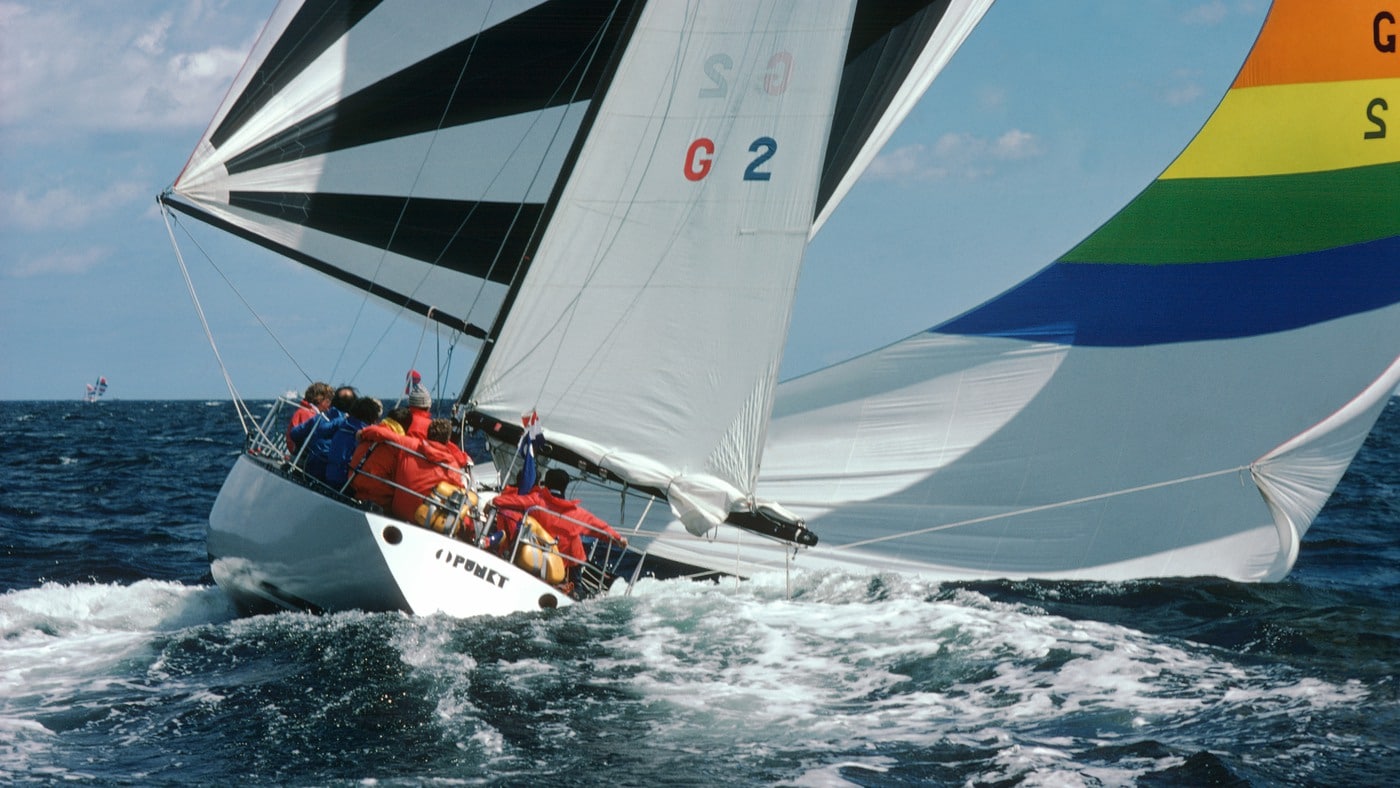
The above is one of the three I.O.R. Racing projects we did based on Baltic 42 hull. Delivered 1975 – 1979.

This 45 footer, “Schorch” is the first “real” custom project, starting from a blank paper, designing and building only one for the client in question. Douglas Peterson did the design and Rolf Vrolijk was involved in the deck and interior layout.
Year 1982 we delivered the “Midnight Sun” project. This was an 80 FT I.O.R Maxi racer. For us this project was a large step in size but also in building technology.
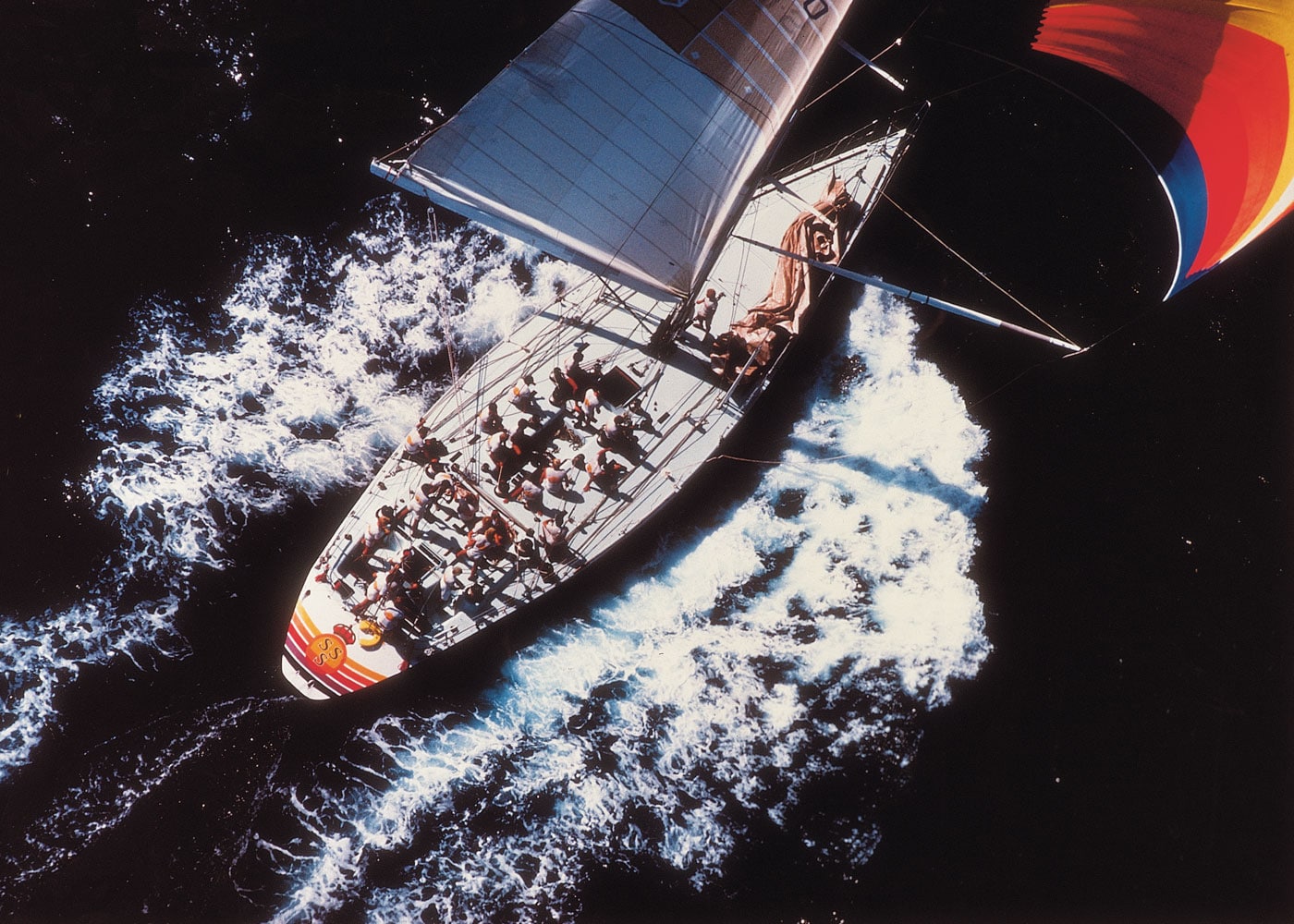
Midnight Sun
A year later we did a very interesting I.O.R. One ton racing machine for a North American client. We used, for the time, high-tech materials and methods and although the yacht was a small size, we learned a few new things through this project. This was a Nelson Marek design.
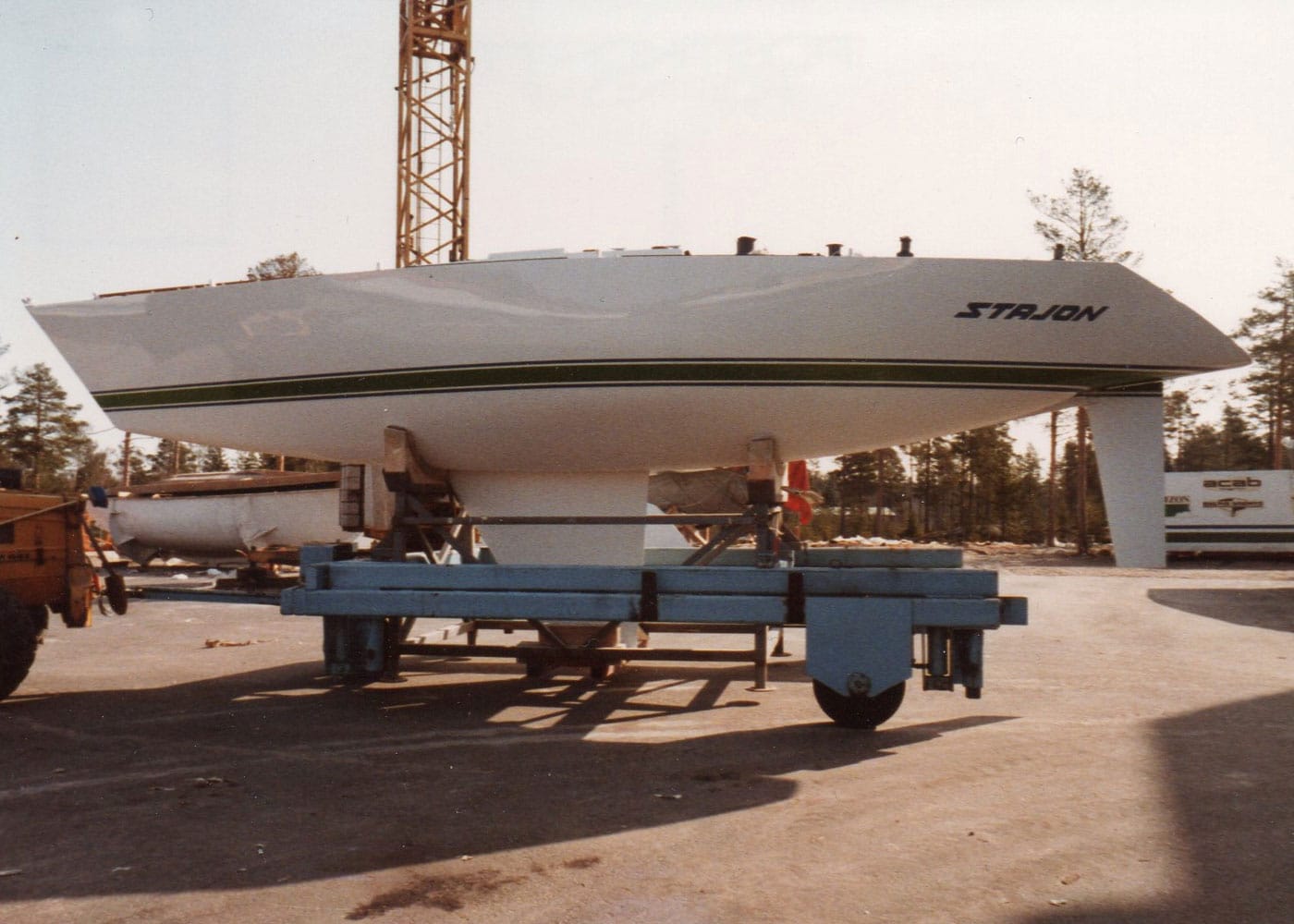
The 38-footer getting ready for delivery. Represent the smaller end of our custom projects.
The same year we were working on two 63 FT sisterships, for two central European clients. We got in contact with these clients via Judel/Vrolijk and they were also Naval architects for these projects. These two yachts were intended for offshore racing as well as some cruising. They had a reasonably good and completed interior, for cruising, but with partly removable interior for racing. The removable interior was not so much for weight saving but for the purpose of making racing sail handling, below deck, a little easier.
We used Vinylester resin in combination with some high-tech unidirectional Kevlar/S-glass fibers. One interesting thing with these two projects was the fact that they were totally identical in construction materials and specification as well as in layout, specification, sail inventory etc. The only differences were the names and the hull colors.
These two yachts were, in the so called I.O.R. Maxi class when they were designed. At that time the Maxi class consisted of boats from roughly 63 Ft size up to 80 FT. I could be wrong, but my recollection is that during the production of these two yachts the Maxi racing class rules was change, not to include handicap calculations resulting in that only approx. 80 footers with a I.O.R. rating of 70.0 could successfully participate.
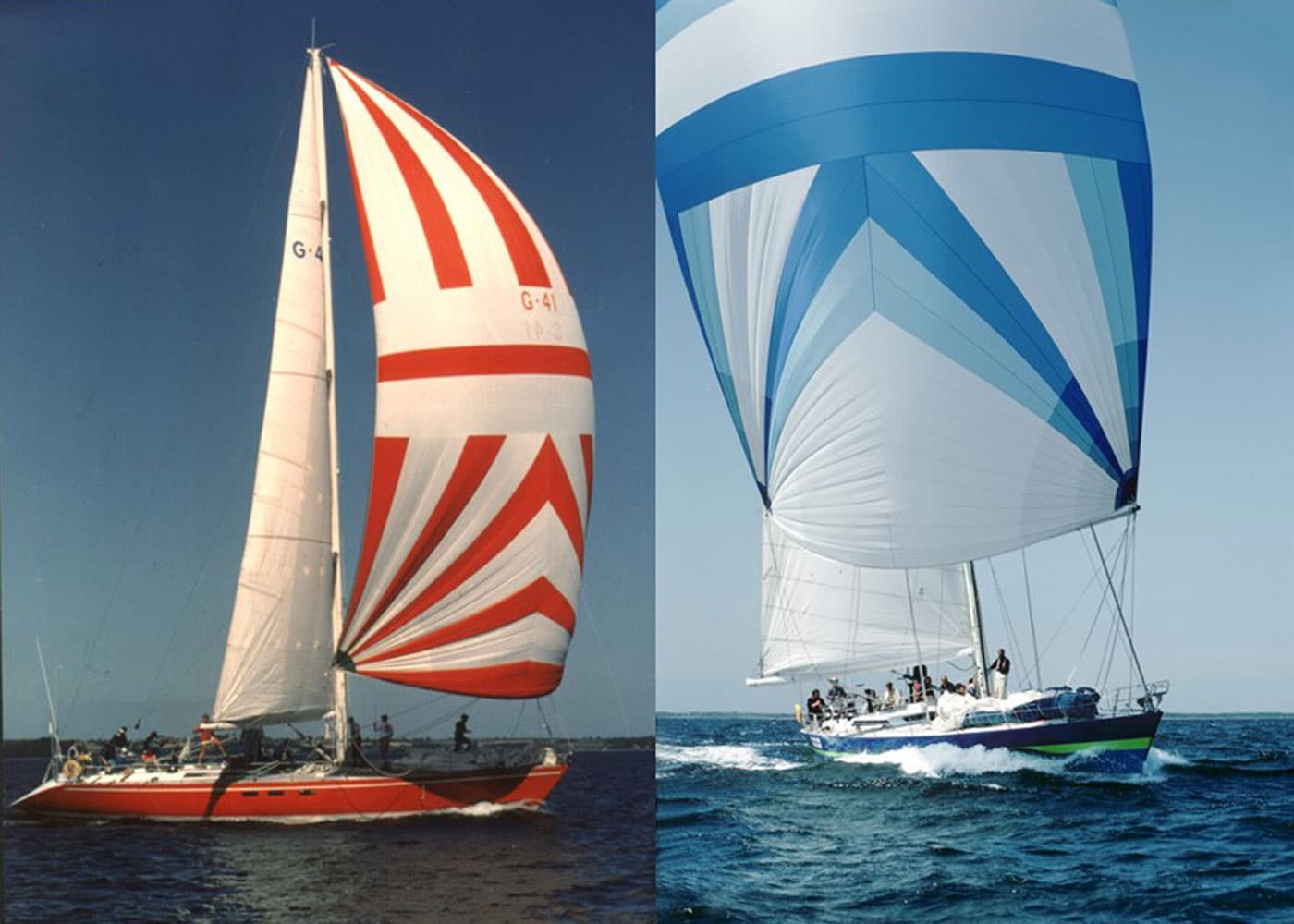
The two 63-sisters
In the mid 1980:s we were involved, as a subcontractor, in a non-yachting project. A deep diving (more than 6000 m) research submarine for exploring some of the deepest spots in the World oceans.
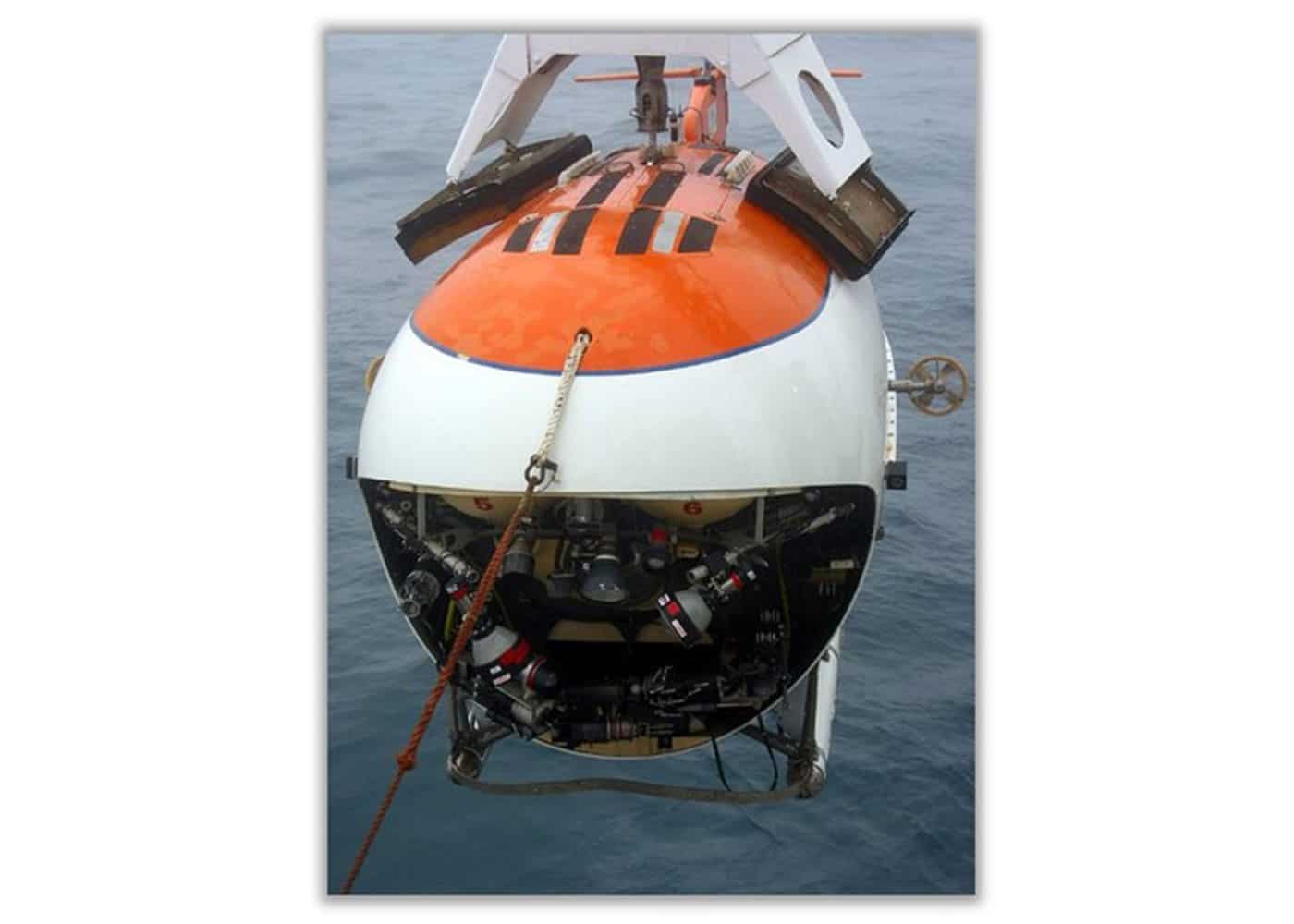
The pressure chamber of this submarine was made in thick metal, in order to take the enormous pressure due to the depth, and we were not involved at all in that. Our part of the project was to produce the composite shell in order to make cover all the technical parts and equipment with a more streamlined shape. You could naturally claim that a laminate like that should be simple to make. But the fact is that if you expose an average laminate to the pressure you have at 6000 m depth the laminate will not be the same after that. All the small, non-noticeable, defects in the laminate will be very visible after the pressure exposure. So not an easy task. If you add to that, that the laminate was a sandwich construction you probably agree that it was a difficult task.
There was a huge level of secrecy around this project, so we were not able, at the time, to use it for publicity. As a matter of fact, the secrecy was so high that the work could not be carried out in our normal facilities, so the work was done in, one of our founders, Jan-Erik Nyfelts home workshop, under his personal supervision and no visitors allowed.
This project required naturally using Epoxy vacuum consolidated laminates also the use of outside laminate expert’s input. Looking at this in hindsight I guess it is fair to say that this project, although not being a yacht, lifted Baltic Yachts Laminate knowledge and capabilities substantially.
The above is just to mention a few of the things we experienced in the early days of our “Custom era”, as mentioned it is not possible to go into detail, too many projects and events. Hopefully if my blog continues I will/can get into the individual projects more in details at a later stage.
As can be seen from the list of projects the sizes did increase from year to year resulting in some of the very best mega yachts in the world. But please also notice that in between the Mega projects we have also built several smaller projects.
From the yards point of view, the custom activities have not only given us contact with some very interesting clients but also with a large number of yachting professionals, Naval Architects, Equipment suppliers, Client project managers etc. Needless to say, that this has broaden and increased the yards knowhow and capabilities.
When building serial production projects compared to custom there are some differences that must be taken into consideration.
Serial Production
With a serial production model, the yard decides the basic concept and philosophy for the project. In our case it was always high-tech, high performance good for cruising but definitely also potential for the racing scene. The consequences of a serial production model are that you are locked into certain limitations, you are locked into a given hull volume and underwater volume (displacement). You can make changes, add weight, do shallow keels etc. but you always need to be aware that there are limitations how far you can go from the original design and still call it a good project. The original basic concept you decided for, no matter how good it was, comes with certain limitations regarding possibilities to make customized modification influencing displacement etc. If you stay close to the original concept and as long as you know what you are doing you can make adjustments but needs to stay within certain limitations.
Custom Projects
With custom projects you don’t offer an existing design and hull shape, to start from. The starting point is a blank paper. You listen to the client, his wishes and priorities, you make all the necessary calculations, loads, layouts, weight calculations etc and develop a design that is optimized for that individual client. Sometimes this is done by the yard, sometimes by the naval architect but in most cases (in a perfect set up) in a cooperation between owner, owners’ team. Naval architect, possible equipment suppliers and the yard.
With custom projects, you are not trying to sell your idea of what a good yacht would be. You listen to the client because it is his dream you are trying to create, not your own.
If a client is in for a very high-performance yacht, then you recommend your best technical solutions in order to achieve this, with weighs saving always being an important factor.
On the other hand, if a client is looking for a high performance and comfortable cruising boat then the recommendations you must come up with are different. But for a cruising boat it is also important to keep weight as low as possible since this will enhance sailing characteristics and comfort. With custom projects the flexibility is there to optimize project in all cases of concepts.
With the serial production there were just fairly small concept differences, from project to project, due to the limitation as explained. On the custom project we have done the spread of concept from racing to cruising have been much larger so for many people it might look as we have departed from our basic concept, and this is not true. We use high tech material and construction plus advanced calculations to optimize and save weights. In our opinion, a lighter construction for both racing as well as cruising gives a better end result. Higher speed, better acceleration, less pitching due to better weight concentration and more comfort.
Baltic Yacht is still true to the original philosophy we had when the company was started. And this philosophy, correctly executed, is beneficial for both racing and cruising projects.
LIGHTER, STIFFER, FASTER, GREENER – TOGETHER
TELL TALES
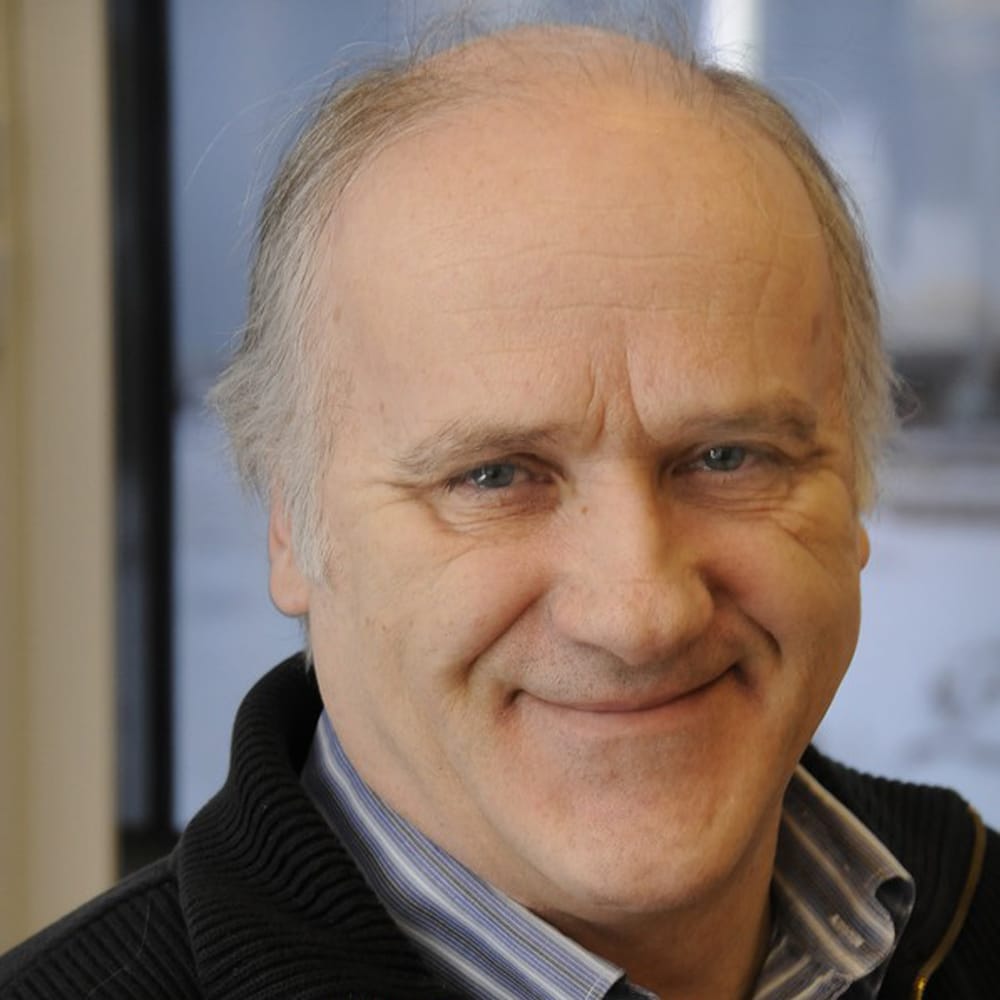
PG JOHANSSON
There can be few yacht builders like PG Johansson, who can boast an unbroken career with the company he co-founded almost 50 years ago. In that time PG Johansson has witnessed every twist and turn of a colourful, exciting and technically pioneering industry accumulating a wealth of fascinating stories, some familiar, some still untold. In this blog PG will be recalling his experiences of the yachts he has built, the people he has met and some of the more unusual events on the journey to turning clients’ dreams into reality.
Would you like to comment on this post or share your own Baltic story? Join our ‘Baltic Yachts Tell Tales’ facebook group exclusive to the Baltic Family.
PREVIOUS BLOG POSTS
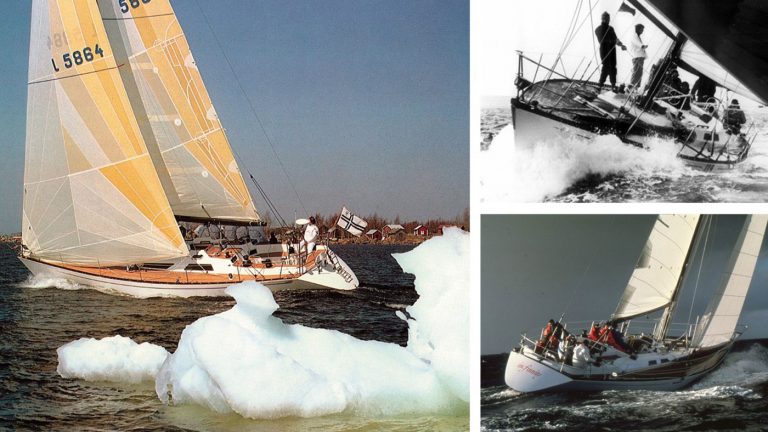
TELL TALES: FOLLOW YOUR HEART
Looking back at Baltic Yachts history and going trough the files and statistics of all the project that has been...
MORE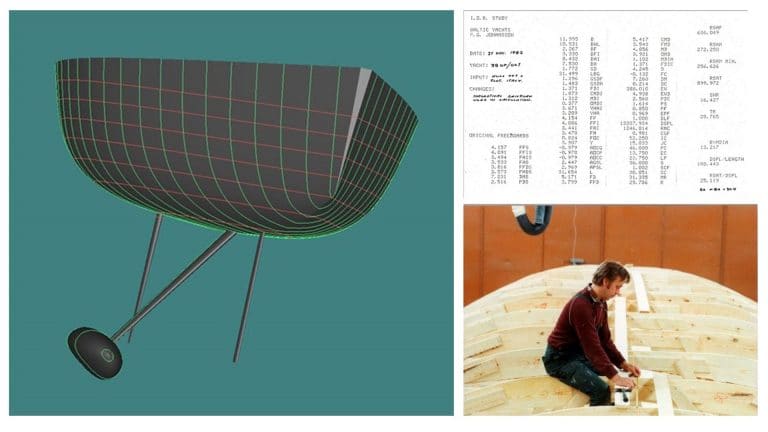
Tell Tales: From paper and pen to fully computerized
Sometimes when looking through old files, drawings, photos etc. it often hits me how much things have developed/changed during these,...
MORE