Tell Tales: The ultimate dream for a yacht builder
10 June 2021
During the, soon to be, 50 years since the start of Baltic Yachts, many extremely interesting projects has been executed. Some large some small most of them challenging but in different ways. Some have been technically very extreme, with use of new materials and methods in order to meet the expectations of the clients. Others very demanding regarding equipment and styling.
To lift some of the projects out of the mass is very difficult. However, one series of projects that stands out regarding technical developments started 1987, when our German agent sold a Baltic 43. That was a start of a series of yachts built for the same client that would be very demanding for Baltic Yachts but also lift the technology levels very high.
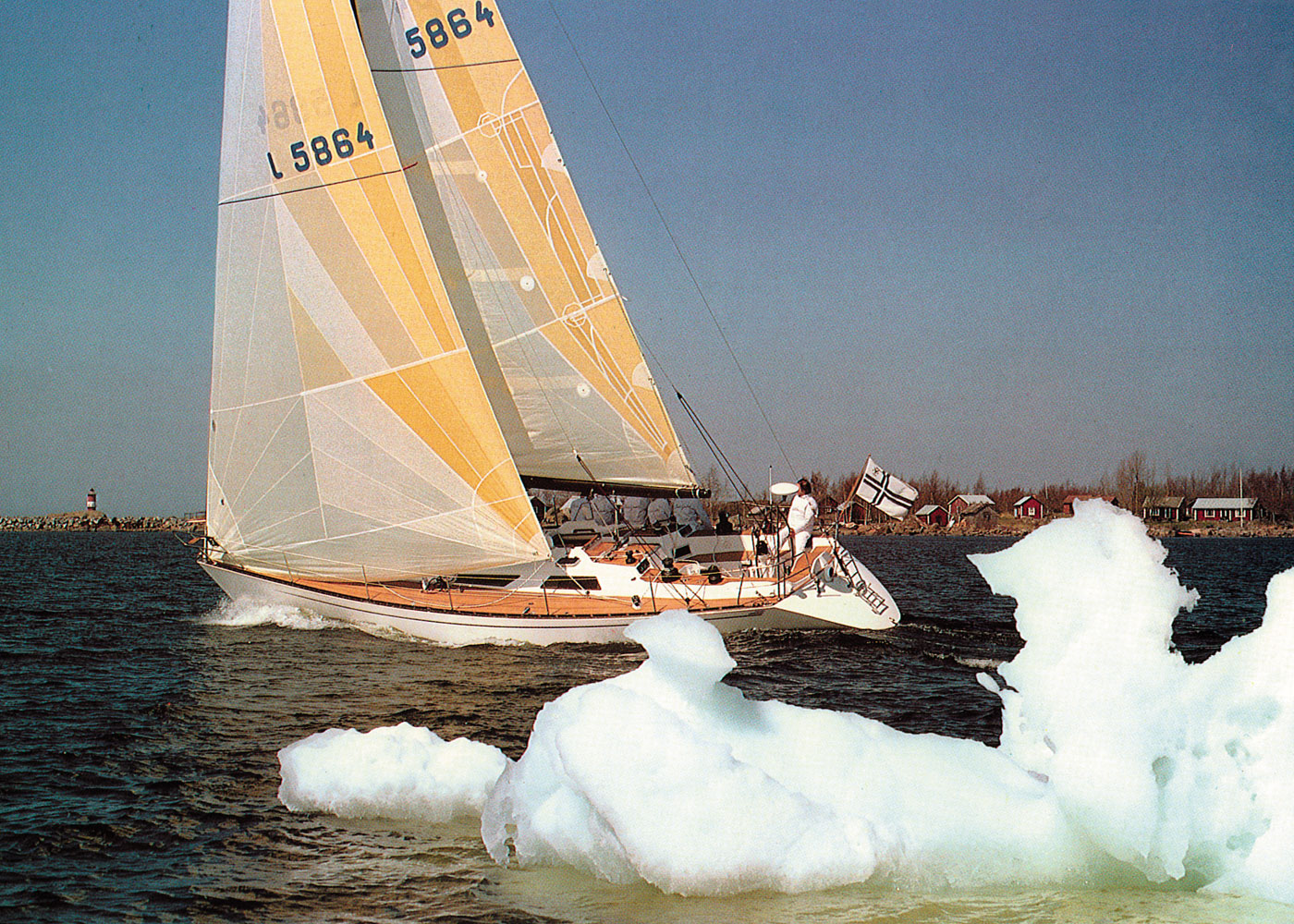
Baltic 43 (sistership) test sailing, early spring, in Finland.
After a couple of years this client started to plan for a new yacht. As a result of various discussions, a contract was signed for a Baltic 52.
The client with a background from a very High-Tech business, interested in High-Tech in general, and with knowledge on weight savings effect, was challenging us to come up with something that would improve not only performance but also durability. This was one of the first projects we did using epoxy resin and vacuum consolidated laminating. This enabled us to save some weight and increase performance potentials. This Baltic 52 was delivered spring 1991 and sailed in German waters for some seasons.
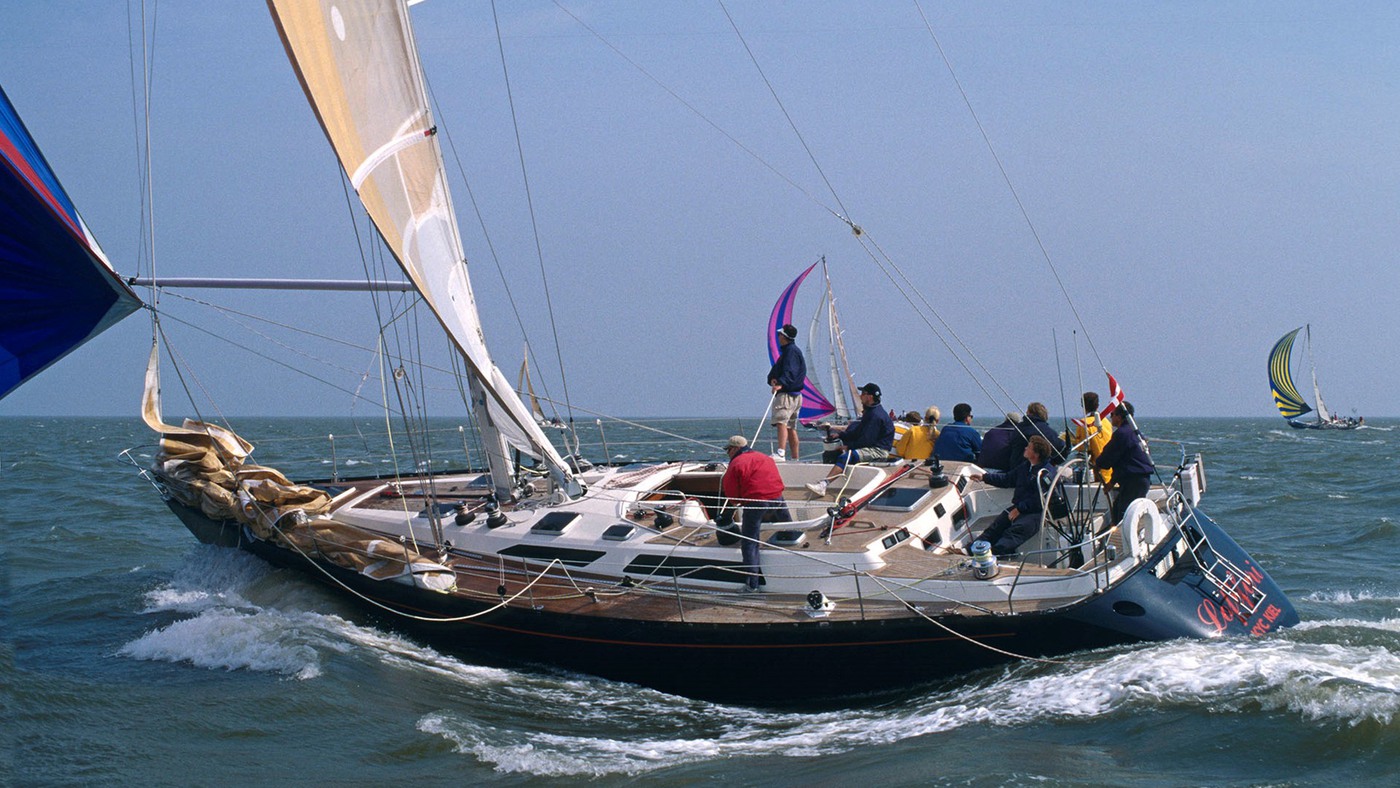
Baltic 52 Loftfari later named Zukunft IV.
The owner later donated this yacht to the Kieler Yacht – Club to be used for sail education and training for the youngsters in the club. It sails under the name of Zukunft IV, and the youngsters have sailed with it actively including one transatlantic race. We also had the pleasure of having them visiting Jakobstad and our yard during one summer. Unfortunately, the yard was closed for the summer holiday, but we showed them around and at the end gave them a Baltic Jacket each, it seemed appreciated. A group of youngsters very well behaved and in good team spirit and very proud of their yacht. Later in the autumn, during the Hamburg Boat Show, we had a good number of young positive supporters, very appreciated.
Sometimes during 1996 the client contacted us showing interest in a 70+ very high-tech super performance cruising project. This owner had, for some time, competed successfully in international racing regattas with so called racing machines, designed by Reichel/Pugh. My recollection is that he did extensive, successful, racing both in the 50 Ft class and a the (80 ft) class. His idea was to take the technology and experience gained for the extreme racing scene and use this to create a second to none performance cruising project.
Together with the owner, Reichel/Pugh, Walter Meier-Kothe (our German agent) and some of our material suppliers a project was developed, contract signed and a super interesting project under work.
The hull and deck laminates were full carbon pre-preg laminates vacuum consolidated and cured at 85°C temperatures in an oven. As sandwich material in both hull and deck Nomex honeycomb was used. In other words, the most advanced technology available at the time. Interior was made using thin Carbon pre-preg sandwich (Nomex honeycomb) panels covered with a thin teak veneer. Extremely light but strong. Equipment through the whole project was selected based on the most technically advanced available at the time. This project, the cooperation with the client and Reichel/Pugh, raised our technical capabilities and capacities, several points higher.
According to our fiber and resin material supplier this was the largest pre-preg carbon laminate in the world, at that time.
This yacht was delivered to the Mediterranean in December 1998 and did its first sailing season there.
Extremely challenging project, interesting and which contributed greatly to the technical development and know-how for us.
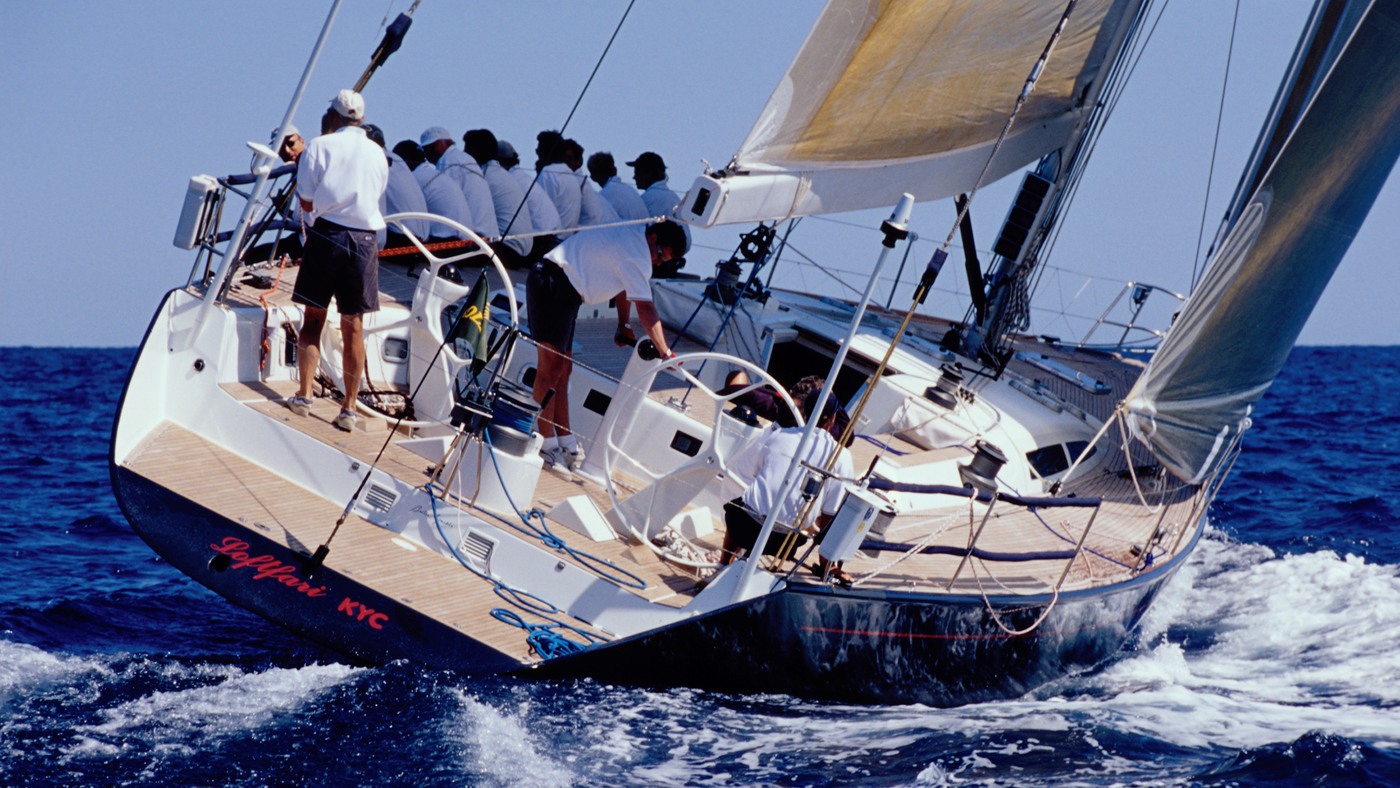
The 70 FT Loftfari
A few years later this owner showed interest in a new project. Very much based on the same concept as the 70-footer but twice the size. The design brief asked the impossible, or so it seemed at first. To build a yacht in excess of 140 feet that would be capable of planing up to speeds of 30 knots or more. The development of this project started 1.5 to 2 years prior to production start with a preliminary base hull design followed by several preliminary layout proposals, specifications and detailed weight calculations all in close cooperation with the owner. Extensive VPP studies were carried out on variations from the base design, lighter, heavier, wider, narrower, higher and lower prismatic etc. In addition, VPP studies were run on Sloop versus Ketch rigs, water ballast version, canting/lifting keel versus deep lifting keel etc.
Together with Walter Meier-Kothe we visited the client several times presenting our work. The client was very active, had very firm challenging opinions and demands and really forced us to do our optimum.
Finally, the client came to the conclusion that this was doable, and he gave us a go ahead. At that time there was no decision regarding the Naval Architect and on the owners request three top Designer alternatives were contacted. In the end he decided for Reichel/Pugh, I would expect very much based on years of successful cooperation he had with them. During the pre-study the size was 140 FT but grew to 147 at the end.
During this process there was many meetings and discussions taking place within our organization. Many of the requests and questions the client had were things that had not been done before hence it took several brainstorming sessions to solve all the issues and make sure we could materialize this project. Not only was this project the most high-tech project ever but for us it was also a gigantic step up in size. Prior to this our largest project had been under 100 FT L.O.A. so not only was this project a technical challenge but also represented operational problems as transport from the yard to Jakobstad harbor, lifting capacities etc.
I still remember the Baltic Yachts management group meeting in which we had to, finally decide if we dared to go ahead with this project, considering the high technical challenges and the enormous size. We were sitting together with Baltic Yachts managing Director, Lisbeth Staffans, or Production Manager Christer Lill and myself. In the end we all agreed that an opportunity like this is so incredibly rare that we just had to take it. This project represented, at this time and still do, something outstanding but we had enough faith in our team to feel confident that we could make it.
So, after approx. two years of calculations, layouts, specifications brainstorming sessions etc. the contract was signed, and the project was under way.
I can only mention a very small part of the thinking and details that went into this project. It would most likely require a whole book, or two, to give it justice. So just to mention a few things.
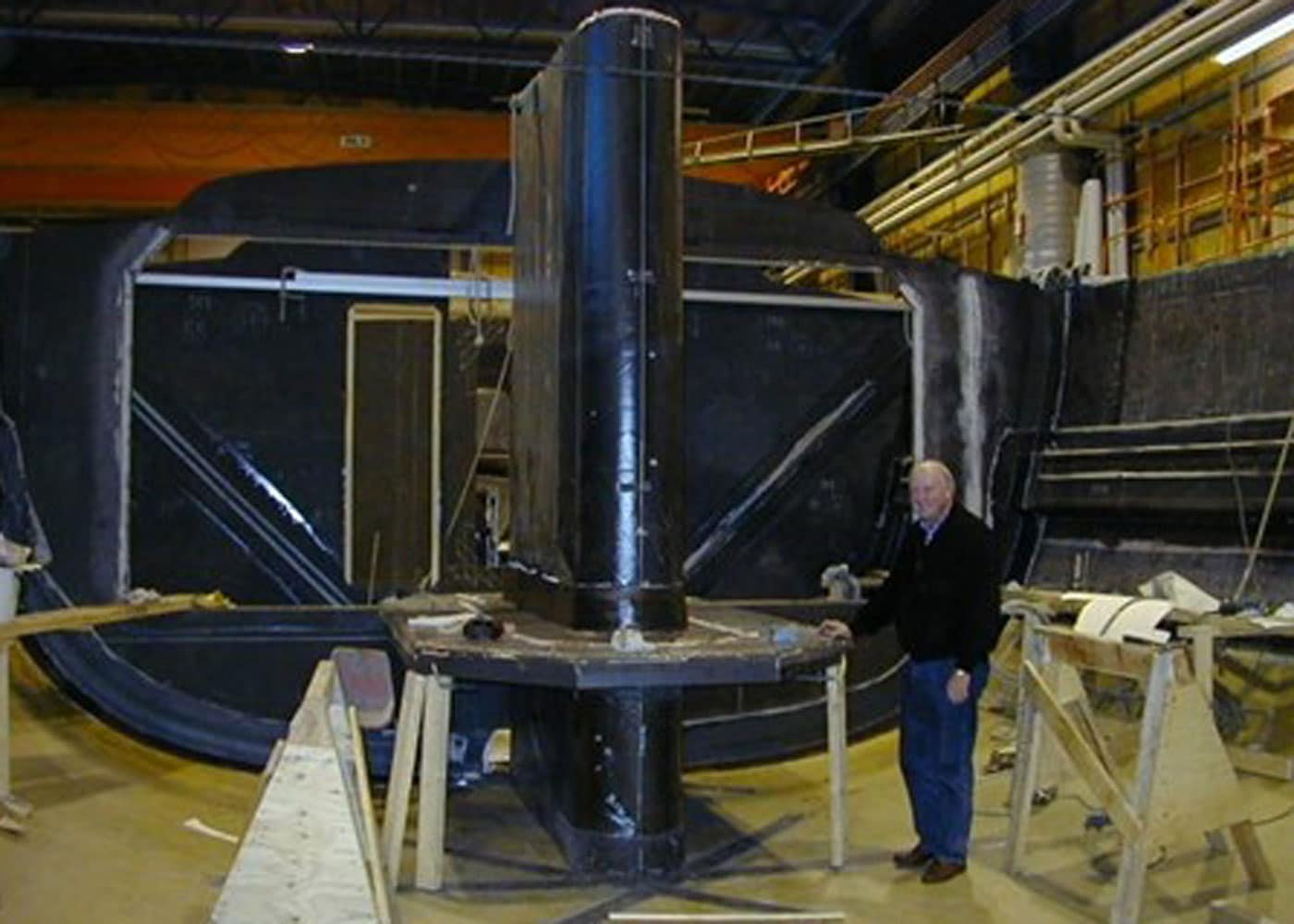
Keel trunk installation on the way. Our agent, Walter Meier-Kothe as size reference.
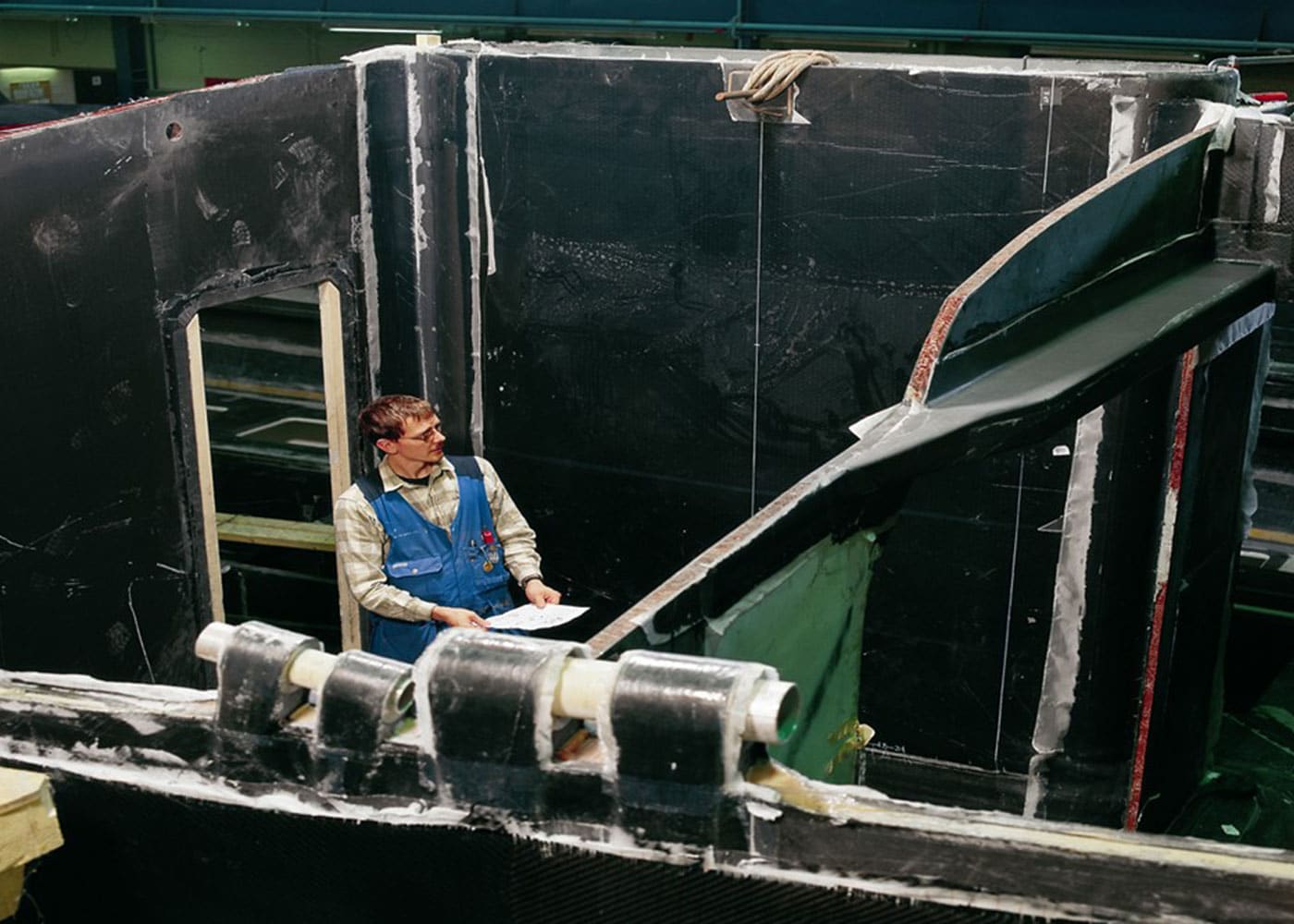
Carbon chainplate construction under work. Actual load approx. 75.000 kg designed for 230.000 kg.

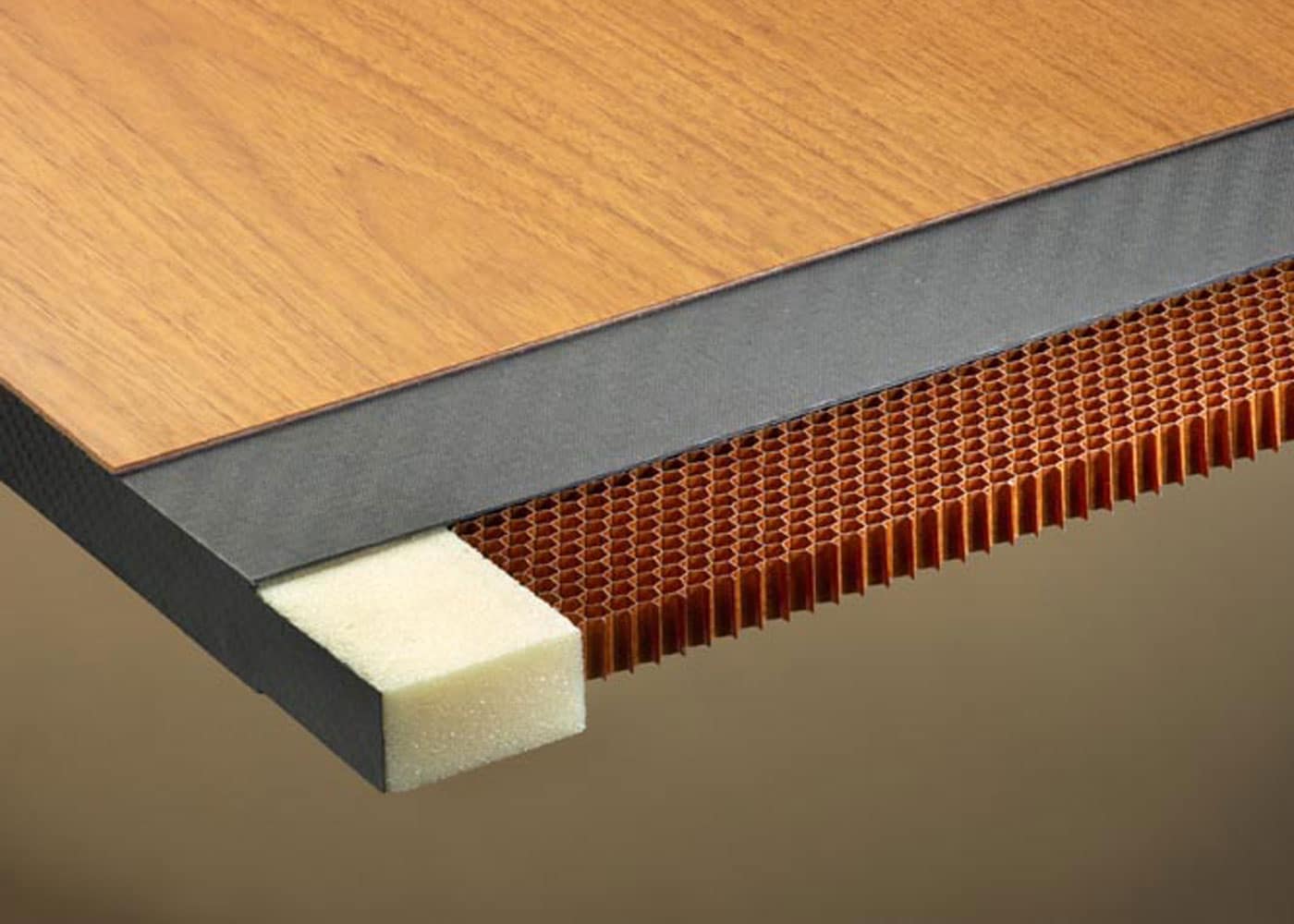
Interior construction detailing.
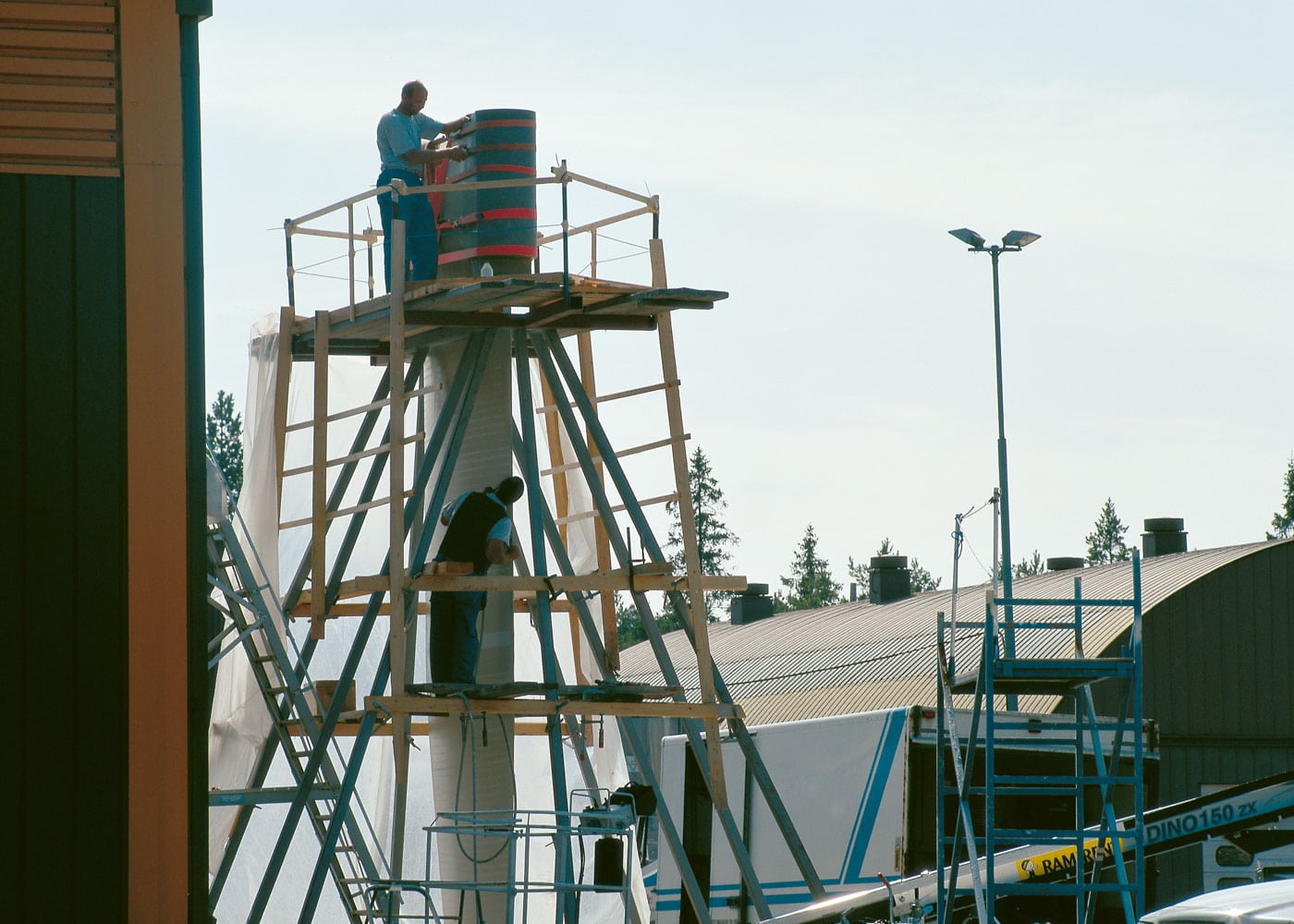
Keel fin under preparation.

A detail, retractable, under water, anchor launching system.
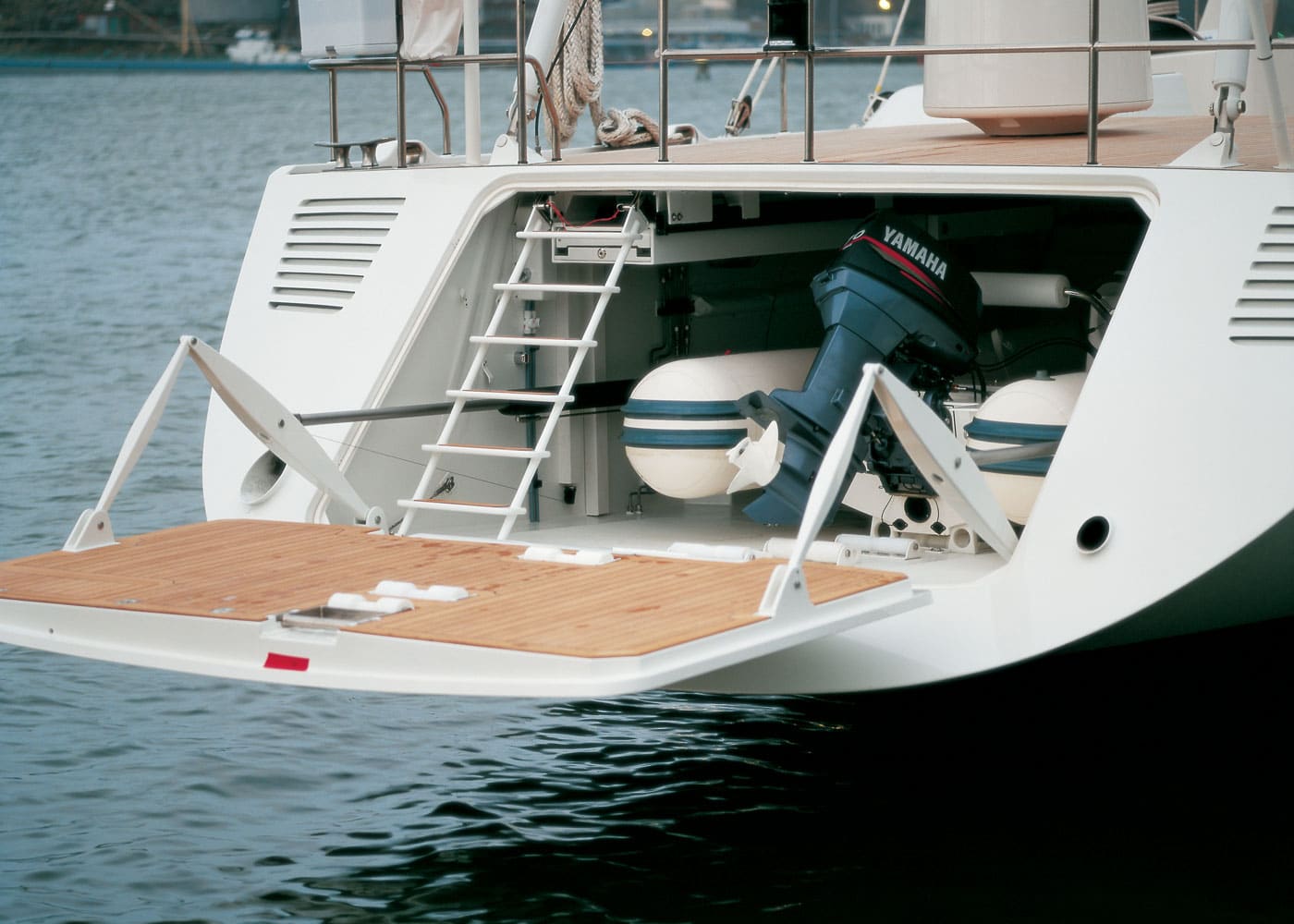
Transom dinghy storage. The lifting arms for the transom hatch, ladder and naturally the hatch itself are carbon construction. The metal parts like the pushpit and lifeline stanchions are Titanium polished to look like Stainless steel.
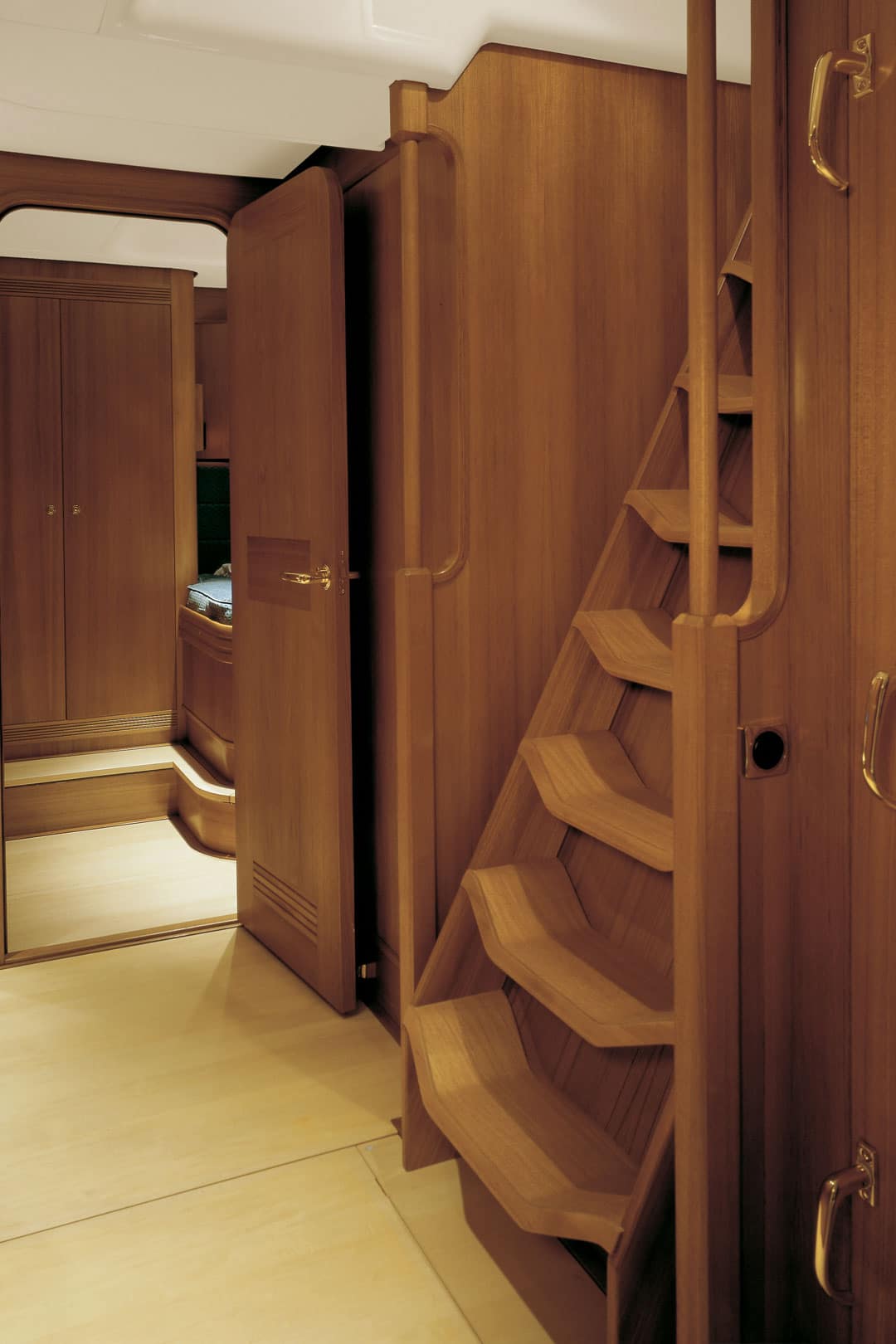
Aft entrance. Looks like a lot of solid wood but…the entrance ladder, sides and steps, is made of thin carbon, honeycomb sandwich laminates with a thin Teak veneer surface. Much lighter than wood and stronger. The vertical handholds are thin carbon tubes with Teak surface. Bulkheads, doors, floorboards etc, carbon Nomex sandwich with thin veneer surface.
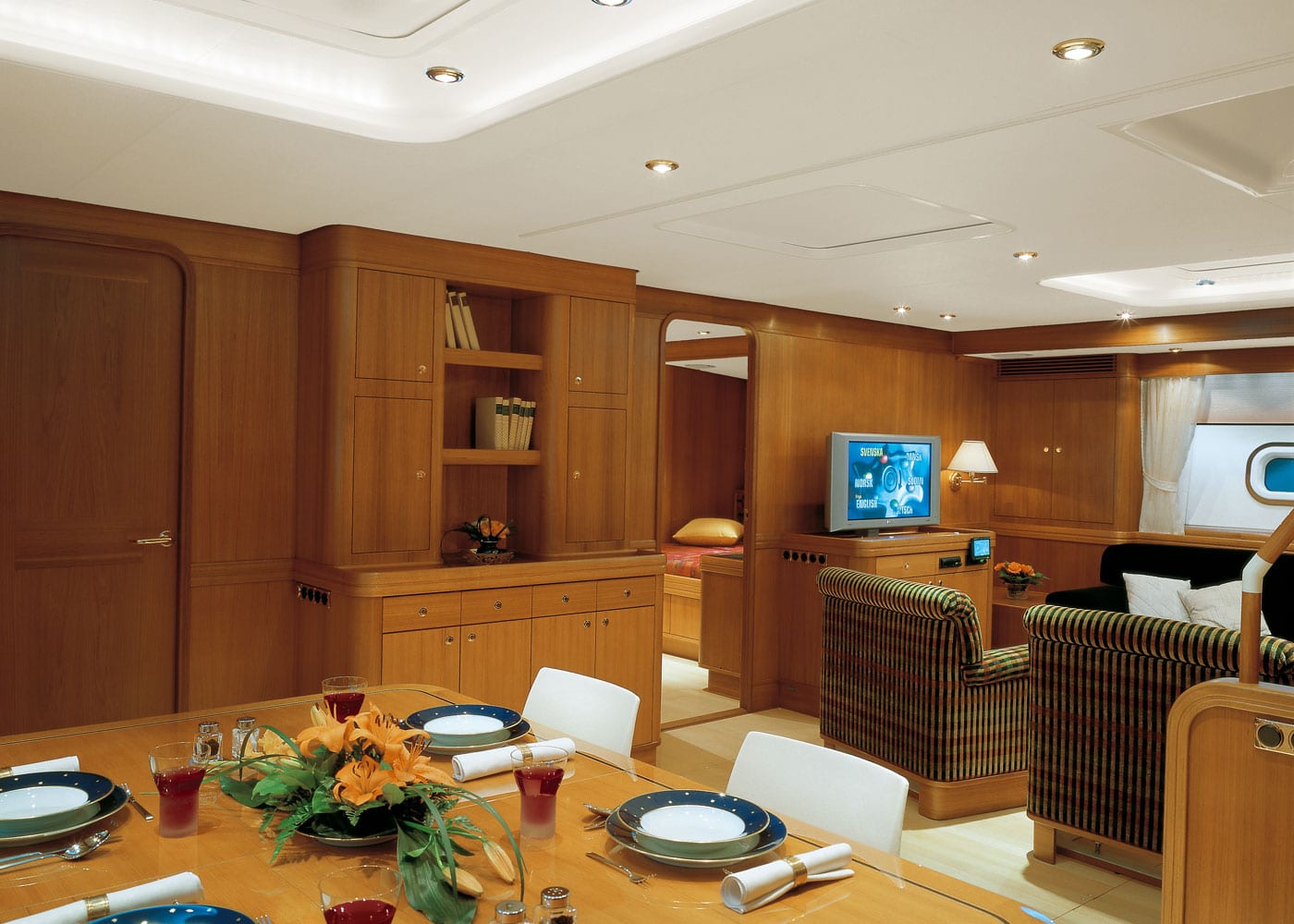
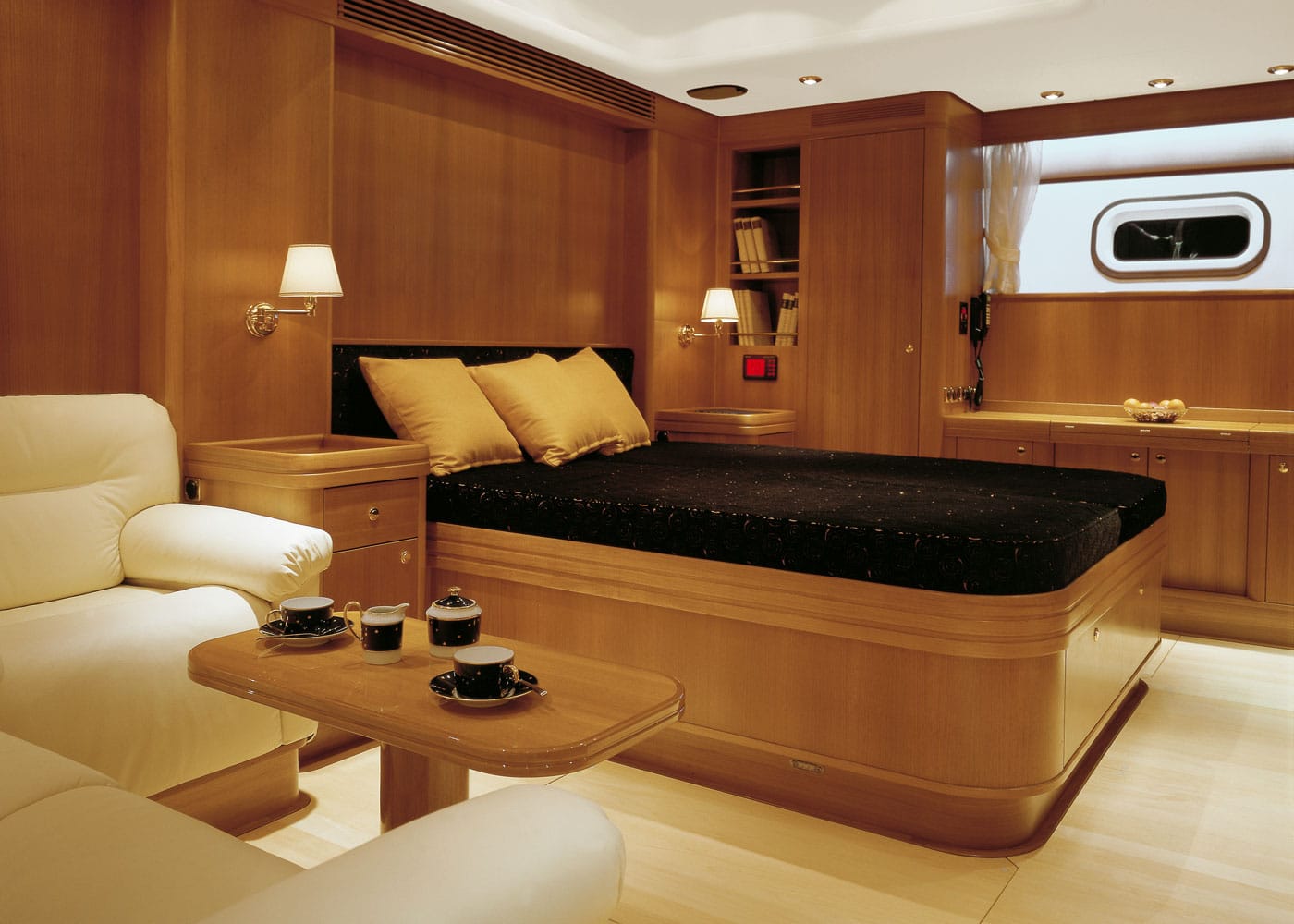
Interior. Has all the comfort that one can ask for but extremely light built.
Baltic Yachts in-house design team, R&J Design, designed the preliminary deck ant interior layouts. Final layouts and styling were made as cooperation between R&J Design and Design Unlimited.
For a performance cruising yacht this project required weight saving philosophy and thinking on a level second to none. The client gave us instructions that whatever ideas we could come up with, during the construction, that would save weight, without sacrificing strength, we should present the numbers to him, weight sawing, financial consequences etc and he would immediately give us decisions if we could go ahead.
A lot of pressure was also on some of our suppliers. As an example, can be mentioned that our Hydraulic supplier; Ward Proctor, supplied hydraulic valve block made of titanium. Also, two large hydraulic pumps/motors (power from engine to prop.) had housing in Titanium. Harken custom made some of the winches to save weight. As I understand that was their base for later development of their light high-performance series. Also, many of the other suppliers were under pressure to come up with lighter construction.
In one of the discussions, we had a question raised: would it be possible find a material heavier than lead which would allow for the bulb size to be reduced, in size, hence reduce the drag. We did some investigation regarding this and found a special material used in space projects, aviation and for radiation protection and balance weights etc. The material was 45% heavier than lead. We did some VPP studies to see the speed gain and got a price estimate. This was one of the very few times the client declined to give go-ahead. If I remember right the price tag would have been in the vicinity of 6 million dollars.
Internally, we informed everybody involved, of the importance of saving weigh. The instruction was that if somebody could come up with ways of saving weight, they should tell us. I must say that our people became very focused on weight saving during this project even to the point of cutting away 2 cm of “overlong” bolts.
Some of the smaller weight savings might seem ridiculous. A weigh saving of a couple of kg should not logically make any difference in a yacht that will weight in the vicinity of 100.000 kg. True but if you find thousands of them, they will make a difference and I am very proud of our teams’ attitude and commitment regarding weight saving on this project.
This project was, for many reasons, very challenging for our team representing several new obstacles. The road transport, 25 km, from the yard to the harbor was a challenge by itself. Parts of the road was closed for the public, traffic signs temporarily removed, refuges removed or filled in etc. Also, another remarkable example of our team’s capability of handle unexpected situations was when we first tested the keel lifting. At this time, we did not have good facilities at the harbor, so the keel needed to be installed and tested at the yard. For that purpose, we had made, outside of the production building, a keel pit to enable enough keel movement. When we started to test the keel, we noticed that the keel pit was not deep enough. Unfortunately, the bottom of the pit did not consist of soil but solid rock. To solve the problem without adding too much time it was decided to use a controlled explosion to remove some of the solid rock. This was done without removing the yacht. May sound a little risky but I can assure you it was done under full control. We had some explosion experts in our team.
To launch, test and finish a project of this size and complexity is a major project by itself. I recall that we had scheduled 2 to 2.5 weeks for this. However, the launching took place late in the autumn and this due to the Finnish climate this represented a problem. The temperature was getting under freezing creating ice in the harbor during nights and furthermore there was almost no wind hence test sailing was not possible. It was decided to move the yacht further south. Visione ended up in Gothenburg Sweden and a team from our yard went down for the final work and tuning.
The 147-Footer Visione was launched late summer 2003. The owner has successfully campaigned and raced with the yacht during all these years and as such giving Baltic Yachts very good visibility and publicity. And even though she has a few years on her neck she is still winning regattas and regarded as the yacht to beat.
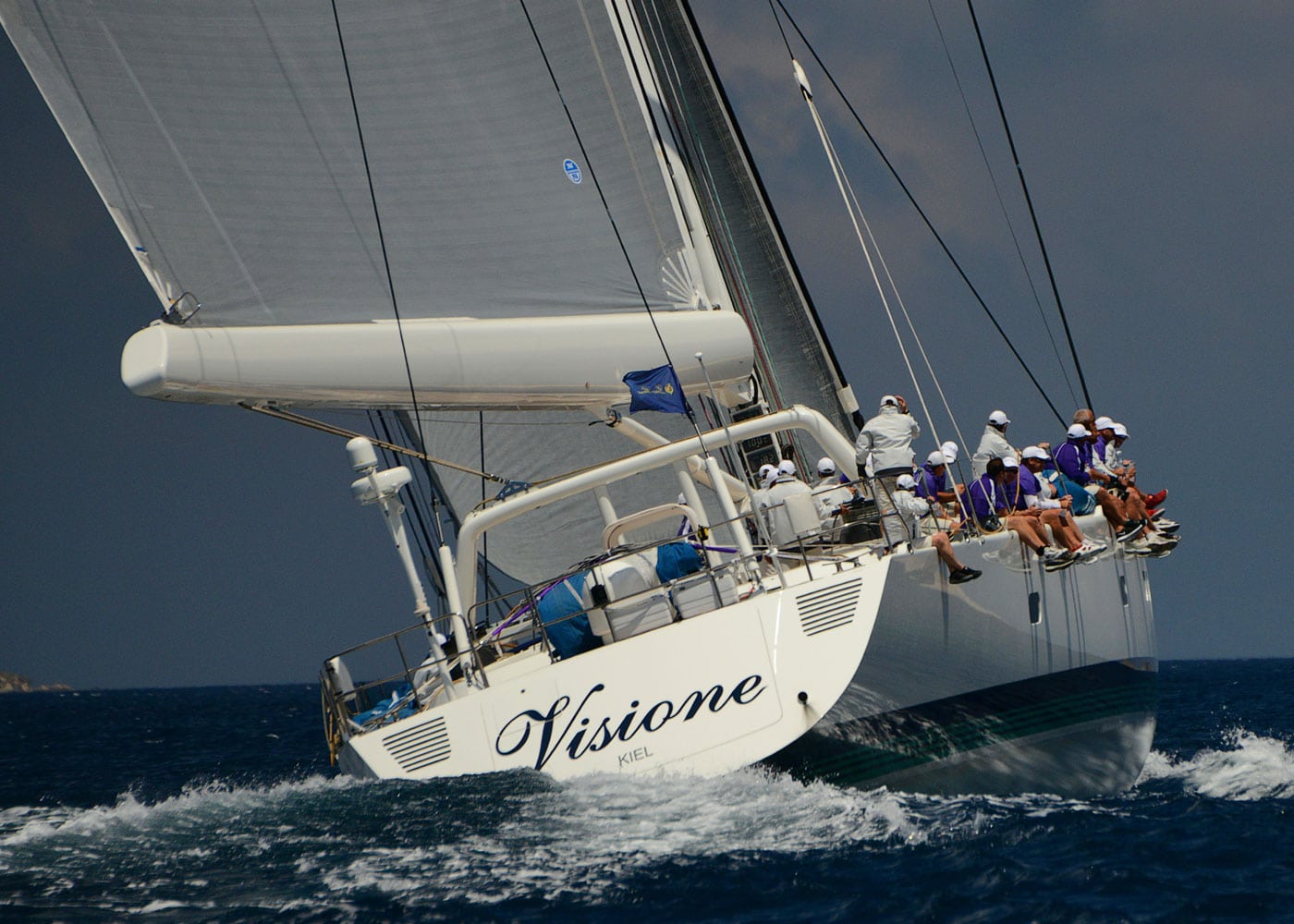
The above covers only a fraction of a fraction of the ideas, thinking and equipment that went into this project. It would be easy to fill two books with information, but this is not the right forum to go into that many details.
Personally, I am very grateful that I have had the opportunity to be involved in a project like this. For most boatbuilders an opportunity like this is something one cannot even dream about.
In a project like this, many people and companies contribute, and their efforts are much appreciated. I cannot list all but want to at least, in this context, name a few.
- Our friend Walter Meier-Kothe. Without him this project would not have materialized.
- Reichel/Pugh Design. Much appreciated
- R&J Design, Roland Kasslin, Jan Wikar who contributed with layouts and calculations.
- Garth Brewer, Captain of Visione.
- Our inhouse project team with Håkan Björström and all the foremen boatbuilders.
- And many many more.
And of course, the whole Baltic team.
But especially, the owner who gave us the unique opportunity and his confidence, in us, to build these yachts but also an owner aware of the fact that when pushing the technical limits like this there will be things that needs to be tuned, adjusted and even replaced in order to reach the goals. And this is to be done with shared responsibility and in a good cooperation and spirit between owner, owners’ team, the yard and suppliers.
The ultimate dream for a yacht builder.
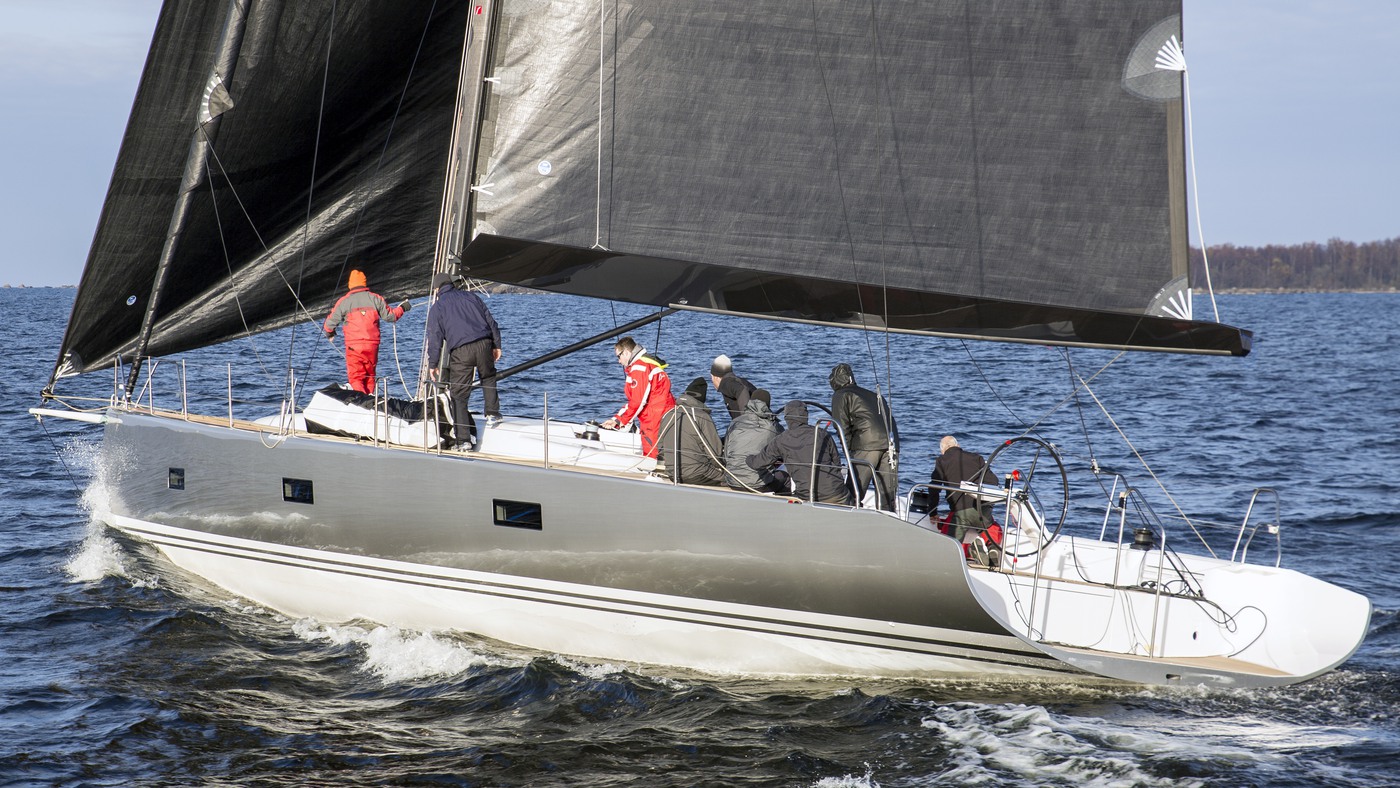
Year 2016 Baltic Yachts launched and tested a Custom 68 FT day sailer, in Jakobstad. After testing the yacht was shipped to California, for the same owner. Needless to say, that it was high performance and high-tech.
TELL TALES
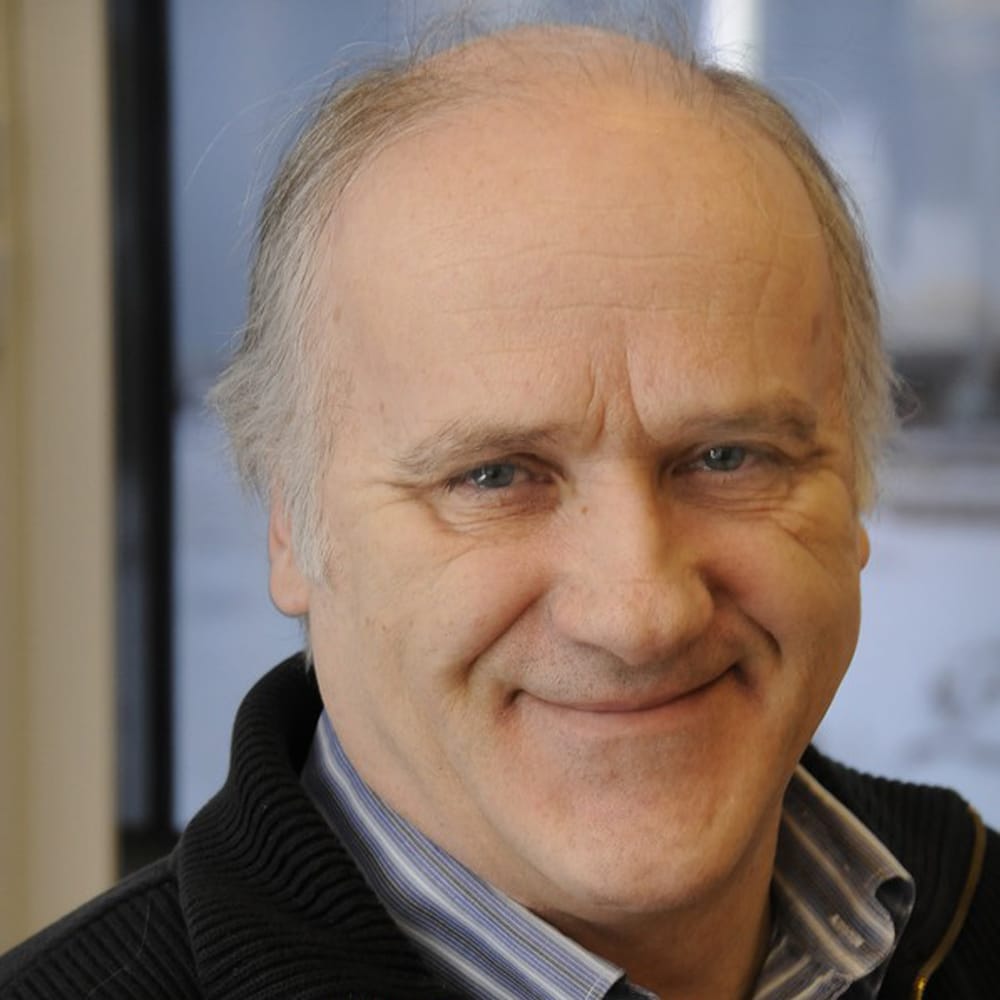
PG JOHANSSON
There can be few yacht builders like PG Johansson, who can boast an unbroken career with the company he co-founded almost 50 years ago. In that time PG Johansson has witnessed every twist and turn of a colourful, exciting and technically pioneering industry accumulating a wealth of fascinating stories, some familiar, some still untold. In this blog PG will be recalling his experiences of the yachts he has built, the people he has met and some of the more unusual events on the journey to turning clients’ dreams into reality.
Would you like to comment on this post or share your own Baltic story? Join our ‘Baltic Yachts Tell Tales’ facebook group exclusive to the Baltic Family.