BALTIC YACHTS’ CUSTOM HATCHES
5 August 2021
Baltic workers’ constant quest to improve design and streamline production has recently been directed at deck hatches with every detail of their complex construction being re-examined
The humble deck hatch might not attract much attention when considering the attributes of a superyacht, but its prime task of keeping apertures watertight cannot be underestimated. Its function is fundamental to safety and comfort and here at Baltic Yachts we are aiming to optimise its design and manufacture.
We are now building our own custom-designed deck hatches drawing on almost 50 years of experience and assessing firsthand feedback from superyacht crews, our Service and Refit teams and our own specialist departments, including plumbing, deck and painting teams.
The company is using full-carbon for strength, stiffness and lightness, more reliable gas-spring struts and lighter, custom designed alloy fittings. The new hatches have been granted DNV-GL class approval.
This move optimizes production by using a single, adjustable mould for the most common hatch sizes, reduce lead times and standardise many smaller components like hinges and locking devices.
In spite of their high build quality, current hatches can still contribute to water ingress, partly because ‘standard’ hatches often have to fit apertures in a custom-designed yacht with non-standard dimensions, deck camber and style. Seal tension, blocked gutter drains and issues with the expansion and contraction of teak deck surrounds are among the contributors to a lack of integrity leading to issues which cause enormous inconvenience and expensive repairs.
The custom hatch product joins our Baltic Best Solutions programme which includes our hull mould technology, our custom, lightweight and ultra-lightweight interior construction options, plus a number of other processes which have benefitted from Baltic Yachts’ design and engineering knowledge and expertise. “It’s all about Baltic detail and depth,” said Project Foreman Mattias Svenlin, an expert in lamination technology, who is heading up the Baltic Yachts Custom Hatch team.

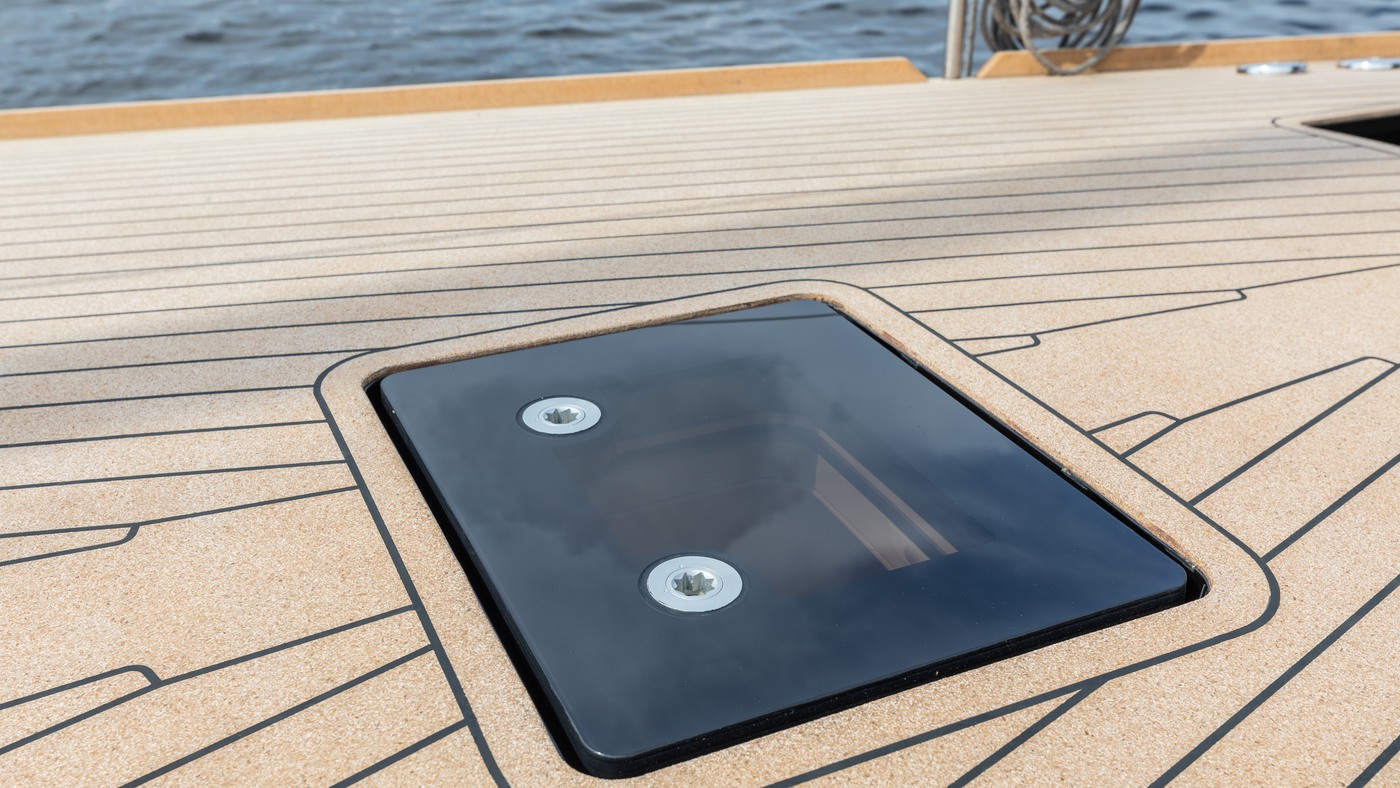
The first yachts to benefit from the new hatches were launched earlier this year. The Baltic 146 is fitted with no fewer than 42 deck hatches in 18 different sizes. The Baltic 117 is fitted with 34 deck hatches customised with classic styling, and the new Baltic 68 Café Racer also benefits from the lighter, more reliable custom product.
Mattias Svenlin explained that while material choice has reduced the overall weight of a hatch by around 15%, design changes are also key. For instance, numerous features such as gutter dimensions and access to drains have been examined and improved, making it easier for crew to clean and maintain.
Gas spring integrity, silicone rubber seal performance, remote electronic operation, hinge and locking device design have all been addressed and by using Baltic Yachts’ in-house 3D printing facility, the speed of prototype development has been dramatically increased and the cost reduced.
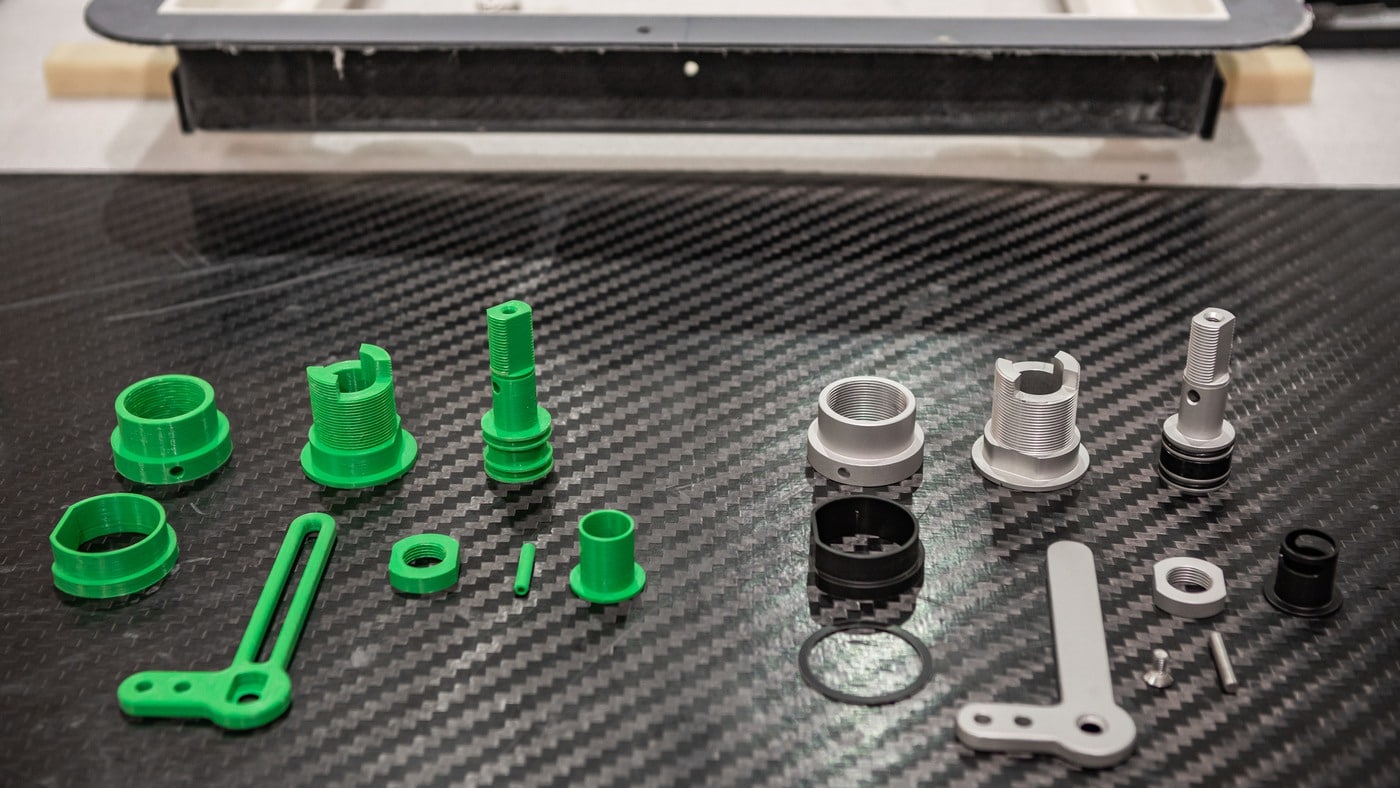
Locking mechanism components are first 3D printed (green) to check design then manufactured in lightweight alloys.
“We can come up with a hinge design, for instance, and within five hours have a working prototype in our hands,” said Mattias Svenlin. Once the 3D printed plastic item has been modified to the satisfaction of the development team it can be sent to a local business partner for fabrication in a high grade, lightweight alloy.
Many existing hatch fittings, including hinges and locking handles, are made in polished stainless steel, but Baltic Custom Hatches will replace this material with high grade alloy or, in some cases, titanium reducing the weight of some items by more than 50%. One component that is unlikely to change is the ‘glass’ itself which for more performance orientated yachts is normally made of polycarbonate or for full DNV-GL classed yachts, three plys of laminated toughened glass.
With so many hatch sizes, adjustable moulds have been built for manufacturing the larger, advanced composite lid and hatch frames and a number of separate moulds for smaller apertures.
Hatch and lid frames fitted to the Baltic 146 Custom are finished as white painted carbon, but almost any finish can be applied including clear-coated, unpainted carbon, timber veneers and coloured powder coatings.
“By building our hatches in-house to custom specifications we will be able to better control the supply chain ensuring hatches create no hold ups in production,” said Mattias Svenlin.
We know Baltic Custom Hatches will help solve the problems which crews currently have to contend with and while the first hatches will be fitted to yachts built by Baltic Yachts, we are hoping to make the product more widely available at a later date.

The weight of some hatch components has been reduced by almost 50% by using carbon and lightweight alloys.
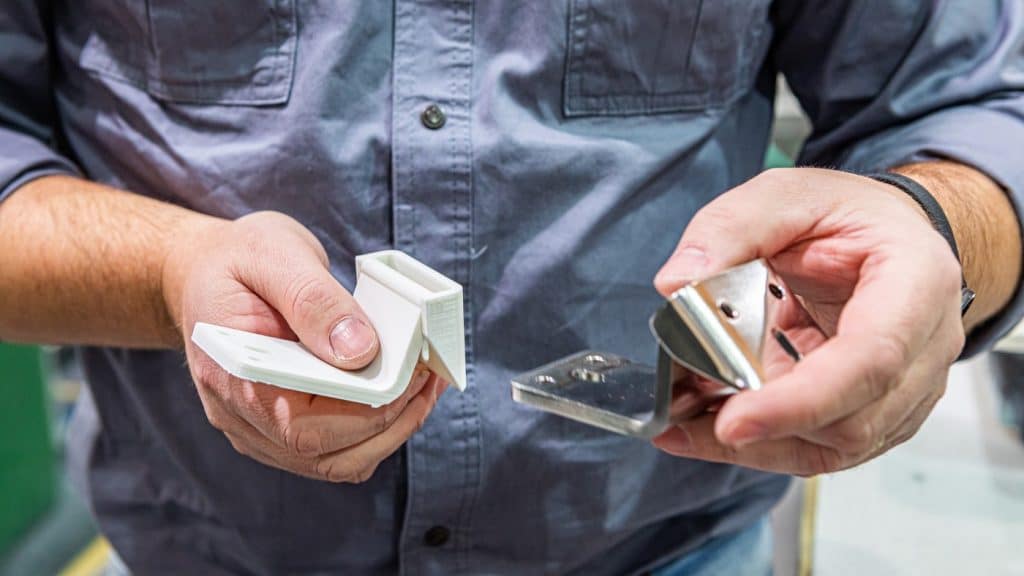
A 3D hinge prototype design was produced in a matter of hours prior to the final metal part being manufactured.
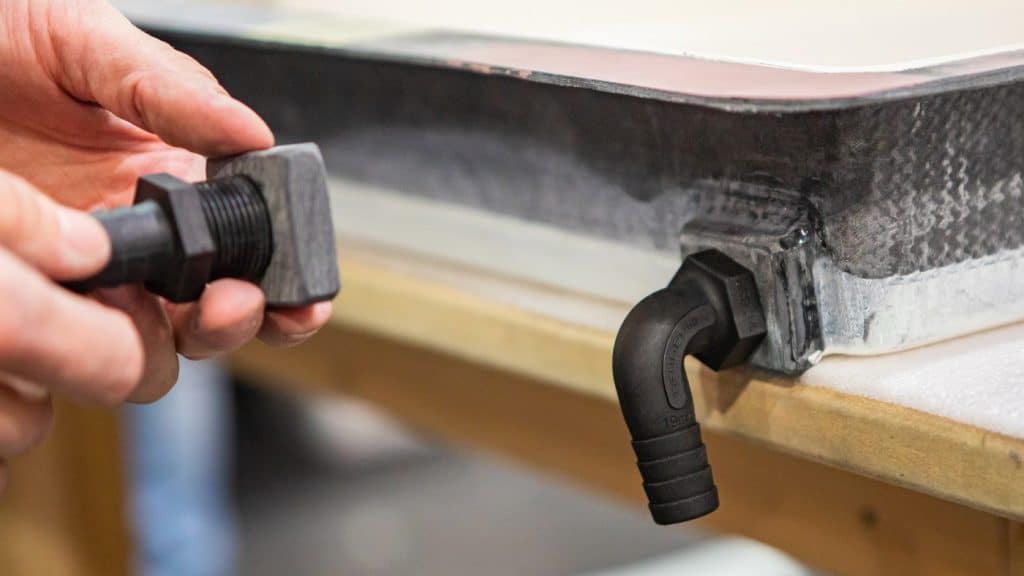
Carbon fibre drainage components save weight and can be removed for ease of cleaning.