TELL TALES: AHEAD OF THE CURVE
6 April 2021
One of the ideas/concepts we had starting Baltic Yachts, was that we were convinced that if we could build yachts lighter, using more modern technology and without sacrificing strength and durability the result would be a faster and easier boat to handle. The laminates were, not the only one but definitely one of the segments that could be improved so going for sandwich construction was the clear alternative. The basic idea, with sandwich construction, is to build up panel thickness and dramatically increase panel stiffness.
This is only simple clear engineering philosophy used for generations in other fields. Take the picture bellow. The steel beam to the left was/is used in many applications, bridge span, overhead cranes etc. Its unthinkable that these beams would be made of solid square steel. The same thinking applies to sandwich construction. The load carrying members, for the steel beam the flanges and for the sandwich the skins, are moved away from the neutral axis and this allows them to do a better work using less weight and much higher stiffness. I know this is simplified but we probably should not go too technical in this forum.
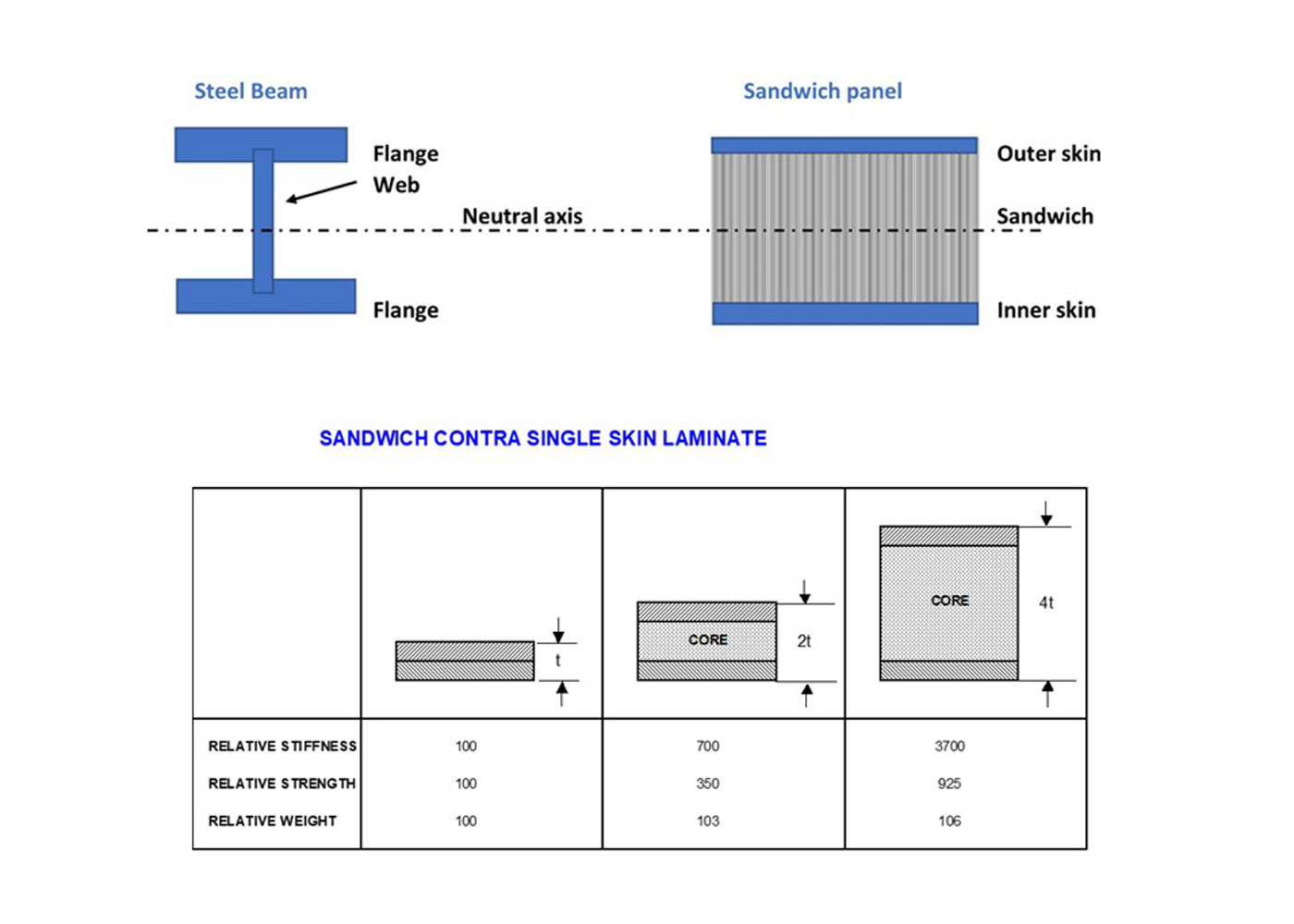
Thinking back on, soon to be, 50 years of Baltic Yachts existence I find it amazing how much things have changed during these years. Just looking at the ways we did our laminates 1973 and comparing with today’s materials and methods, the development is, to say the least, enormous.
In 1973 all, fiber technology laminates were hand laminated. You had a female mould applied dry fiber mats/rowing and rolled by hand resin into these fibers. And the resins used was polyester.
Most yards used solid laminates consisting mainly of woven rowing’s and chopped mats. The woven rowing was the structural ingredient, and the chopped mat was there mainly to reduce print through from shrinking of the resin concentrations caused by the woven rowing. If you did not have enough chopped mats you could, after some time, clearly see the woven rowing pattern through the gelcoat. The chopped mat reduced print through but added a lot of weight and adding only minimal, if any, strength to the laminate.
At the start of Baltic Yachts, one of the things we wanted to improve, was the way laminates were done.
At this time there were already a few yards that had moved into sandwich type of laminates and we were keen to go in for sandwich construction and further develop laminating systems.
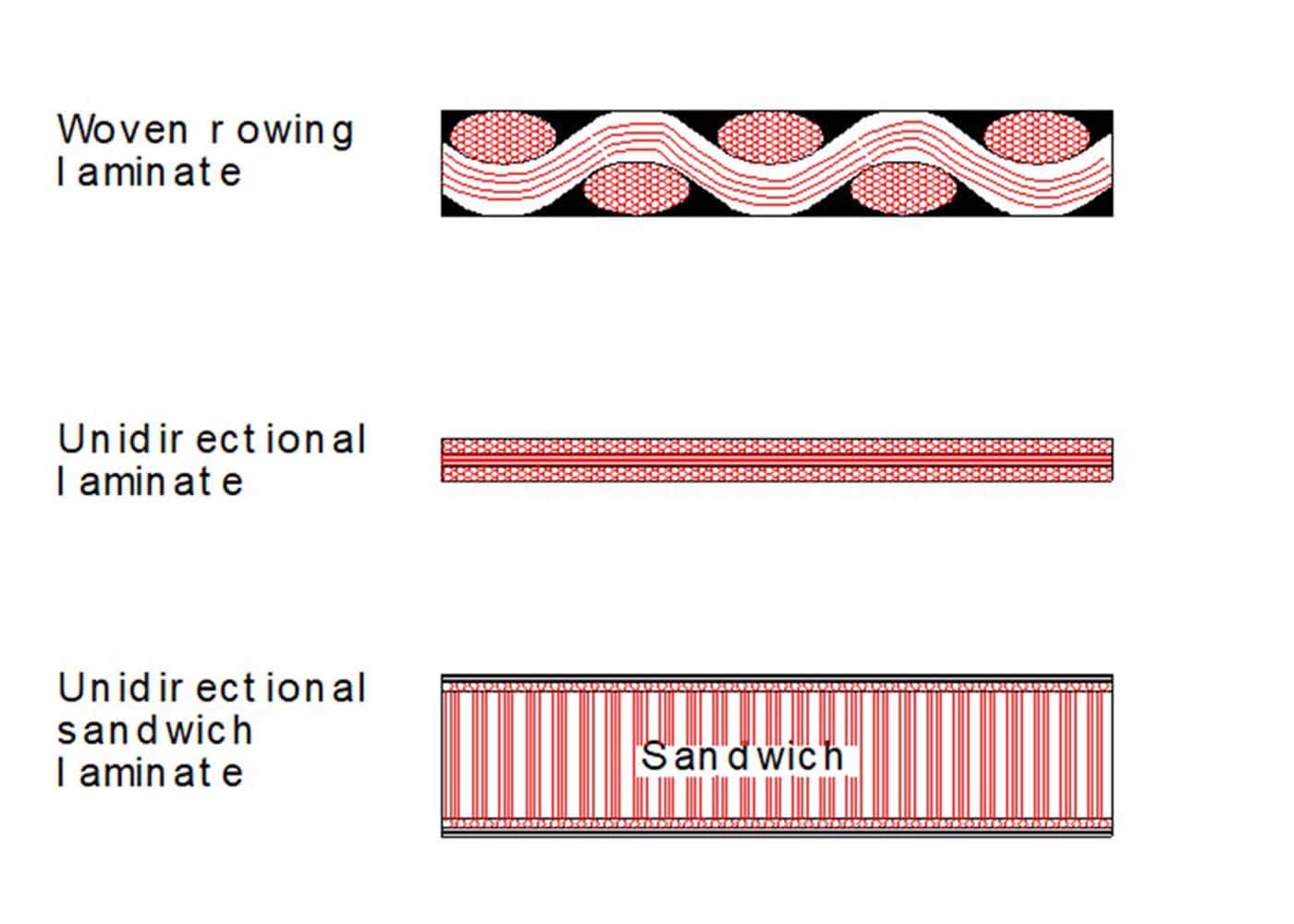
As can be seen from these very schematic pictures (not in scale) the “Woven roving” laminate has a lot of “weak spots”. The fibers in the laminate are not straight but “curves around” inside the laminate. This means that when load is applied to the laminate the resin must stretch a lot before the fibers start to take the loads. This creates a laminate that flexes much and a high risk of microscopic cracks in the resin. These microscopic cracks will allow water to penetrate the laminate and substantially increase the risk of osmosis. In a laminate the fibers are the load carrying members and the main purpose of the resin is to glue the fibers together. To have the fibers bent is from a structural point very bad. You can compare with a bridge span made of concrete. The iron reinforcements in the bridge span would be useless if they would be bent around inside the concrete, they need to be straight and sometimes even pre-tensioned. In principle the same applies to some extent, for laminates.
In the “Unidirectional laminate” all fibers run in the directions of the loads and the fibers will immediately take the load. There are no “weak points”. The only disadvantage, in some applications, is that unidirectional laminates do not build up thickness in the same way as woven roving do hence lower panel stiffness. This is more than compensated when going to sandwich construction.
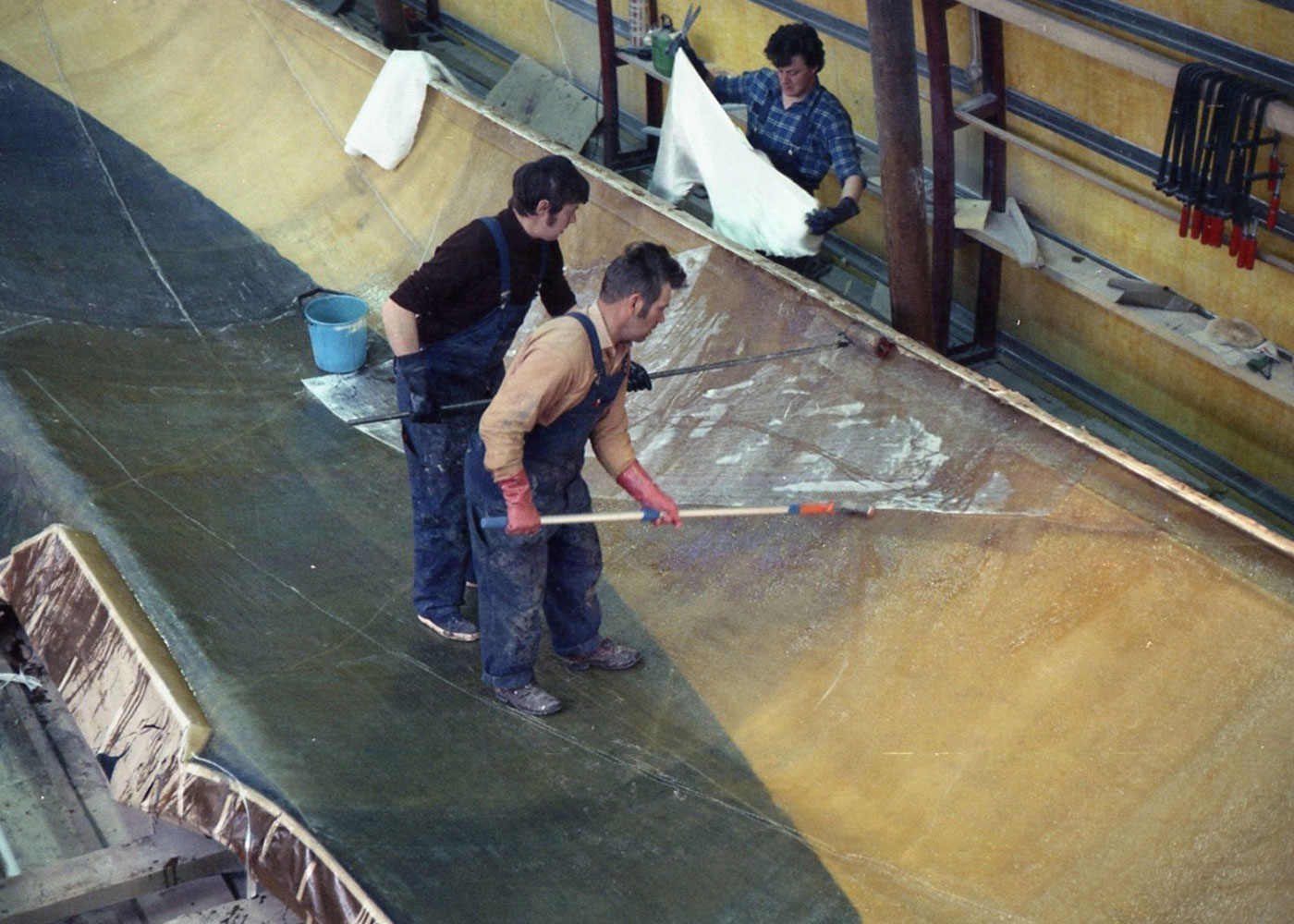
Laminating in 1973
Laminating 1973 looks very primitive comparing with today’s way of handling laminates but at that time using special uni-directional fibers in combination with sandwich construction was top of the line.
During 1980: s materials and methods developed but most laminates were still so-called hand laminated. I remember we did a few custom yachts with a very special super unidirectional rowing consisting of S-Glass Kevlar combination. Material was imported from USA and was considered of such a high standard that a special import license was required. At this time, we also used Vinyl ester resin in some of the more advanced projects.
In the 1980: s Epoxy started to be used in some projects and at the same time vacuum bagging was introduced. Vacuum bagged laminates, those days, were still hand laminated. Epoxy was “rolled2 into the fibers by hand including a peel-ply (removed when laminate was finished) and a perforate plastic film and an absorption layer plus a vacuum bag. Vacuum was applied and the excessive resin was sucked into the absorption layer, hence a better resin to fiber ration was achieved. In addition, the Epoxy had much better properties that previous used resins.
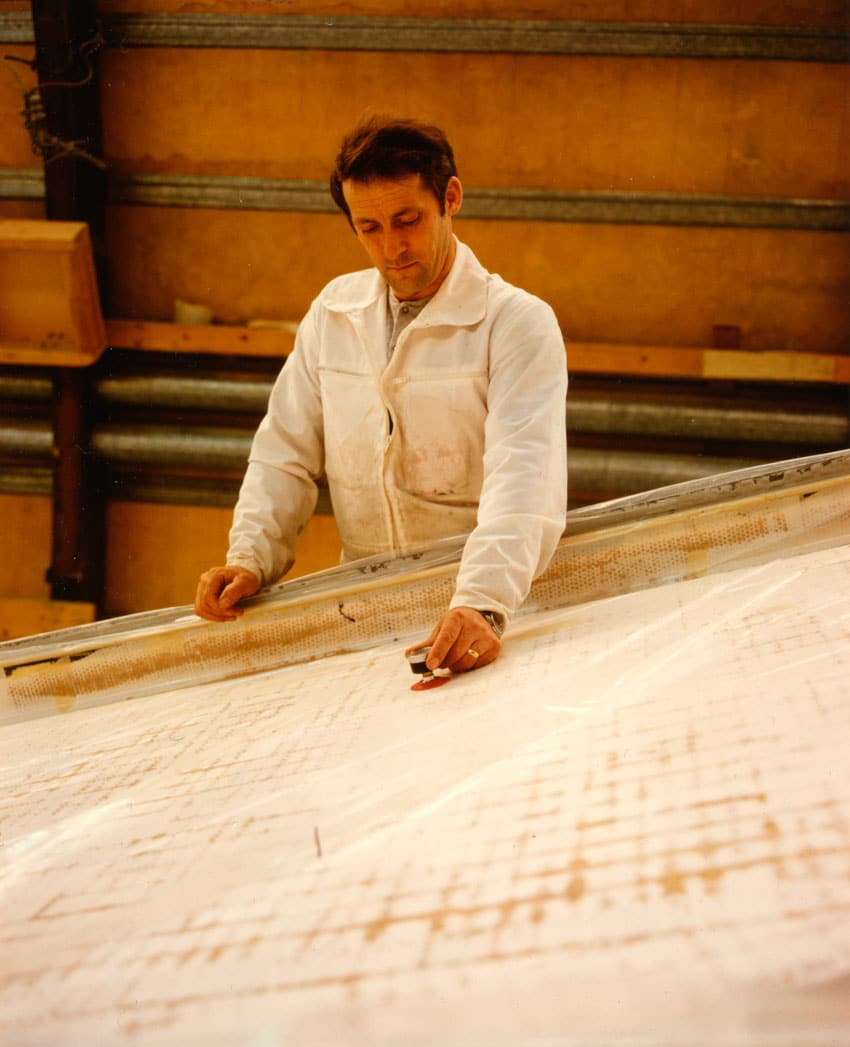
To reach correct strength and quality properties the Epoxy laminates, although room temperature cured, needed to be post-cured in temperatures 50 – 60 C for several hours, mostly over-night. This also resulted building ovens around the laminates.
Carbon fibers started to be used in some applications. First in special high loaded areas and later also in the main laminate.
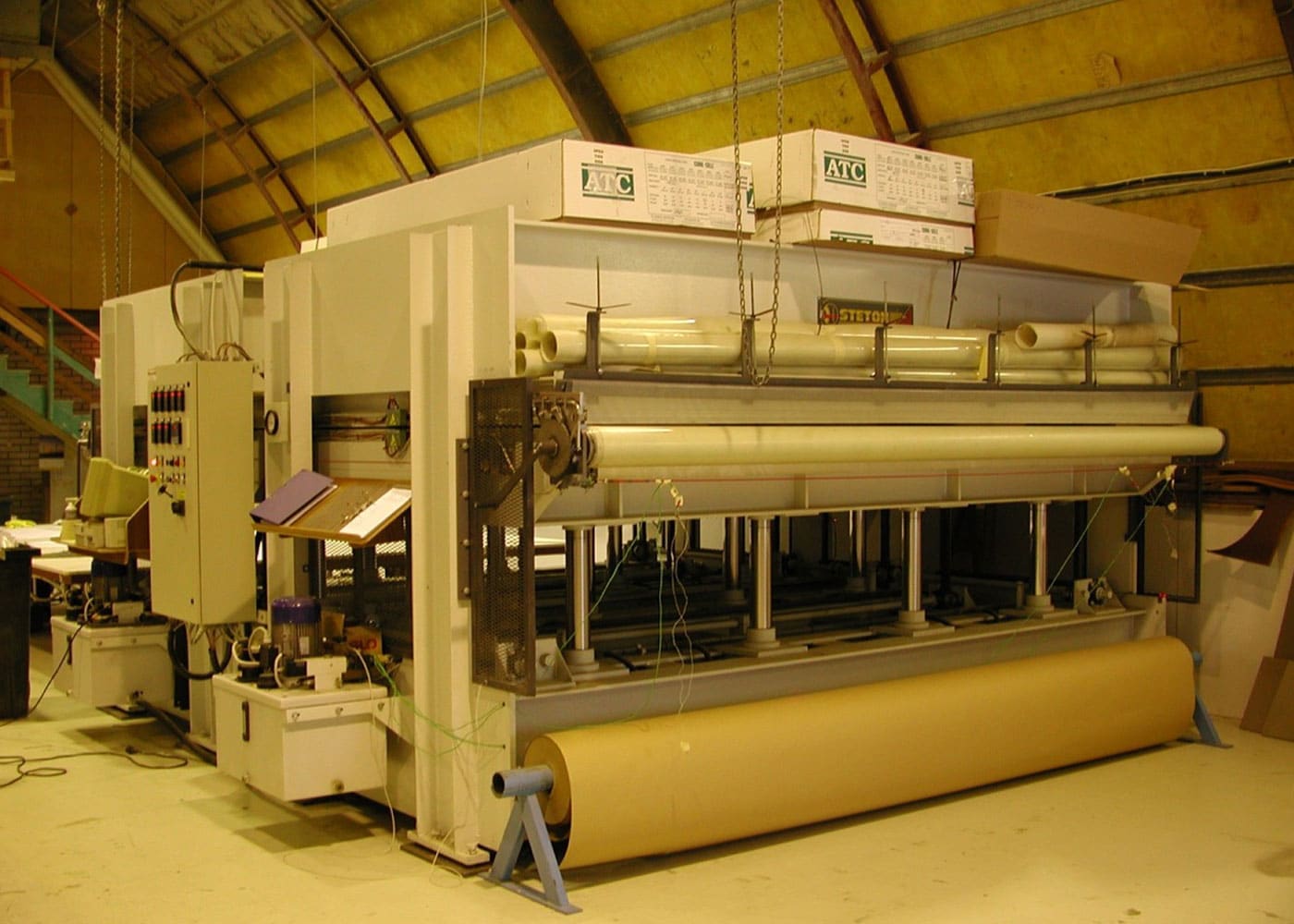
We had also acquired, custom made for us, a hydraulic laminating press with heated upper and lower tables. This allowed us to make flat panels using much higher pressure that vacuum could produce and at the same time achieve post curing at higher, controlled, temperatures. This press was also later used for pre-preg laminates.
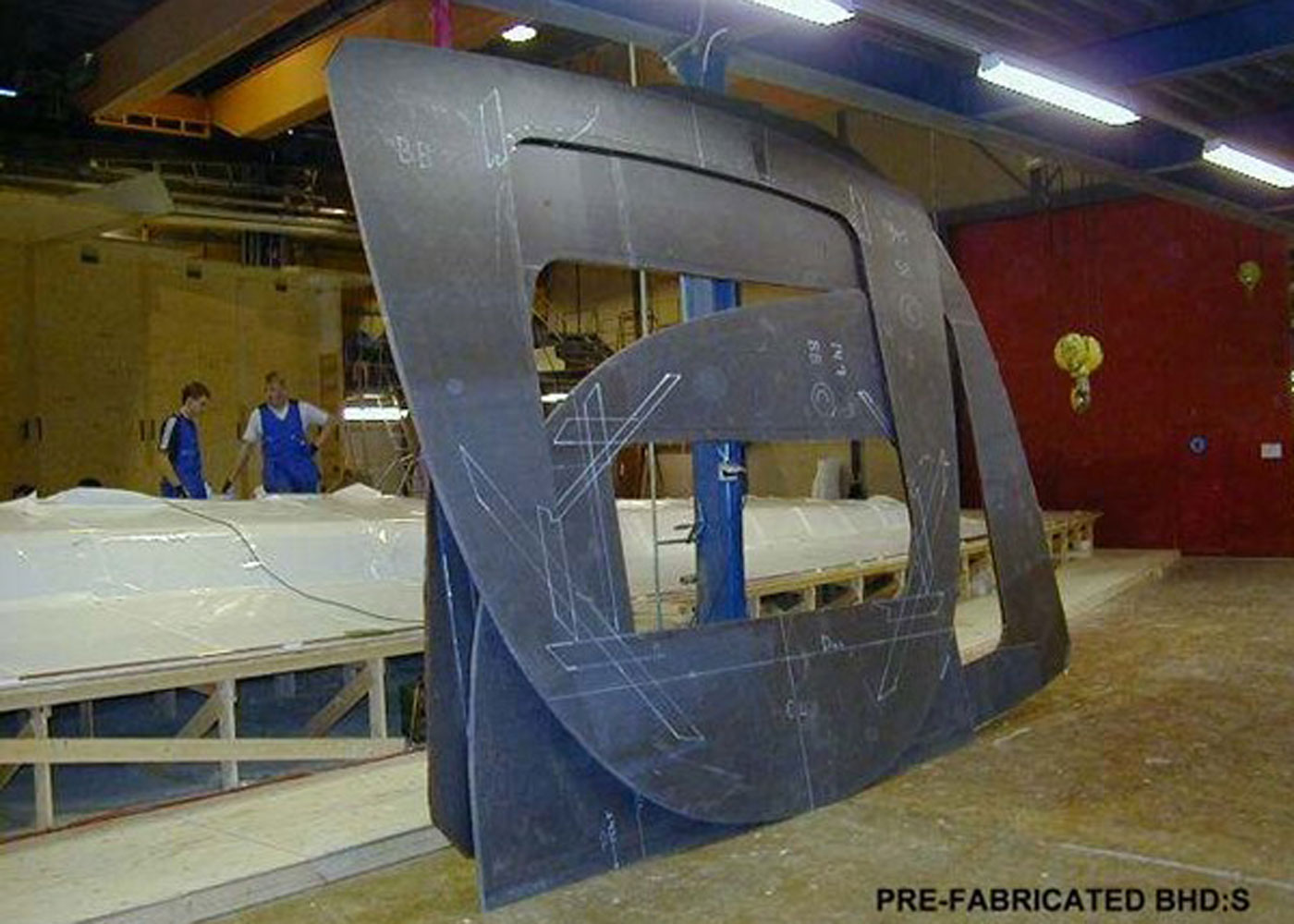
A prefabricated Bulkhead with all extra reinforcements included.
In the 1990: s we did our first “full carbon” hull and deck for a custom 67-footer. We were told by our material supplier that this was at the time the largest Epoxy-Carbon laminate in the world.
Another method that also was in use is the so-called vacuum infusion method. Dry fibers were applied in the mold plus a “flow media” and over that a Vacuum bag. Resin was den sucked into the laminate by vacuum pumps. But, as with any other methods, this could also be done in varies ways hence required some knowledge to get the optimum result. A good system if correctly performed.
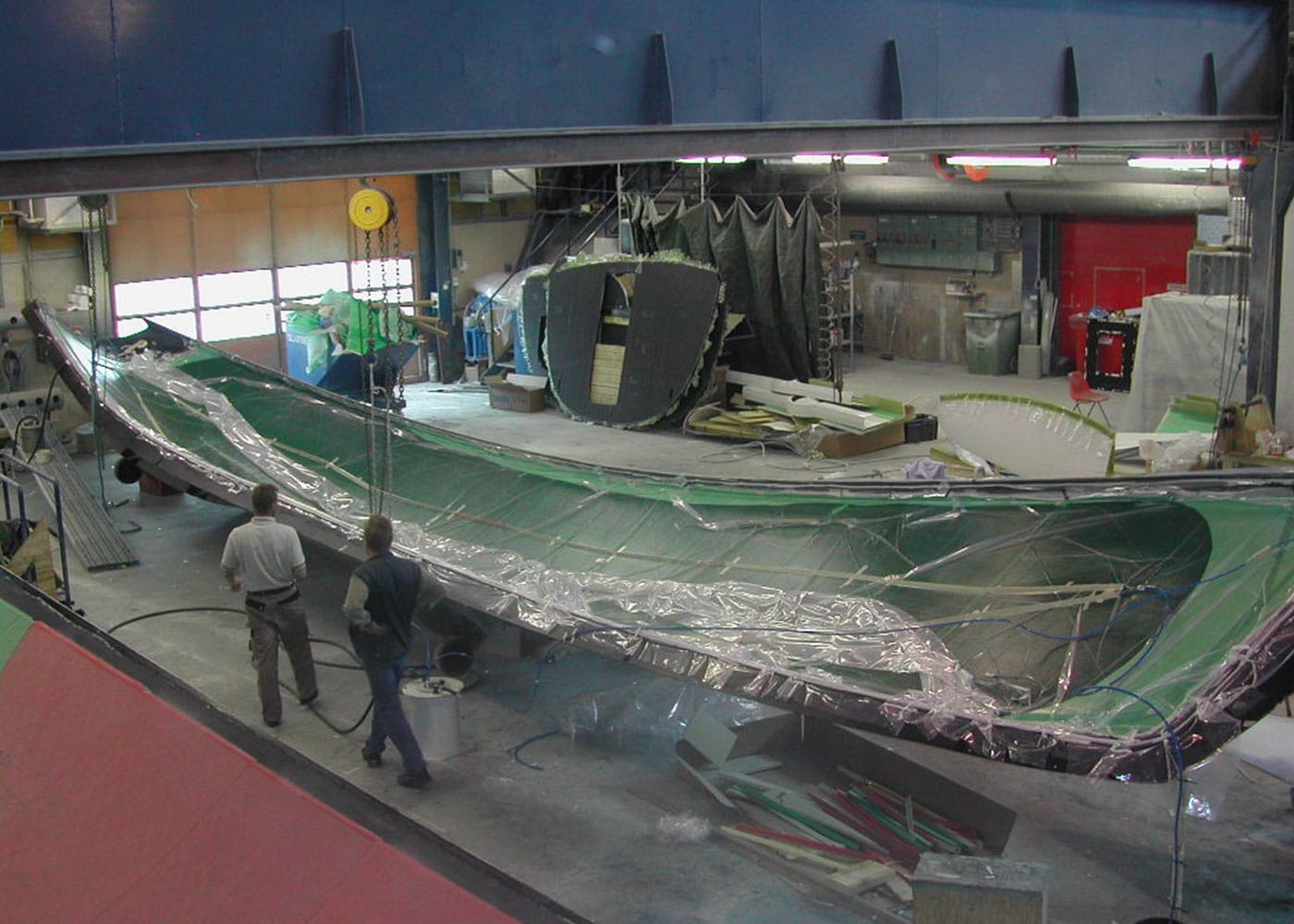
Hull side, probably for a Baltic 56, is vacuum infused.
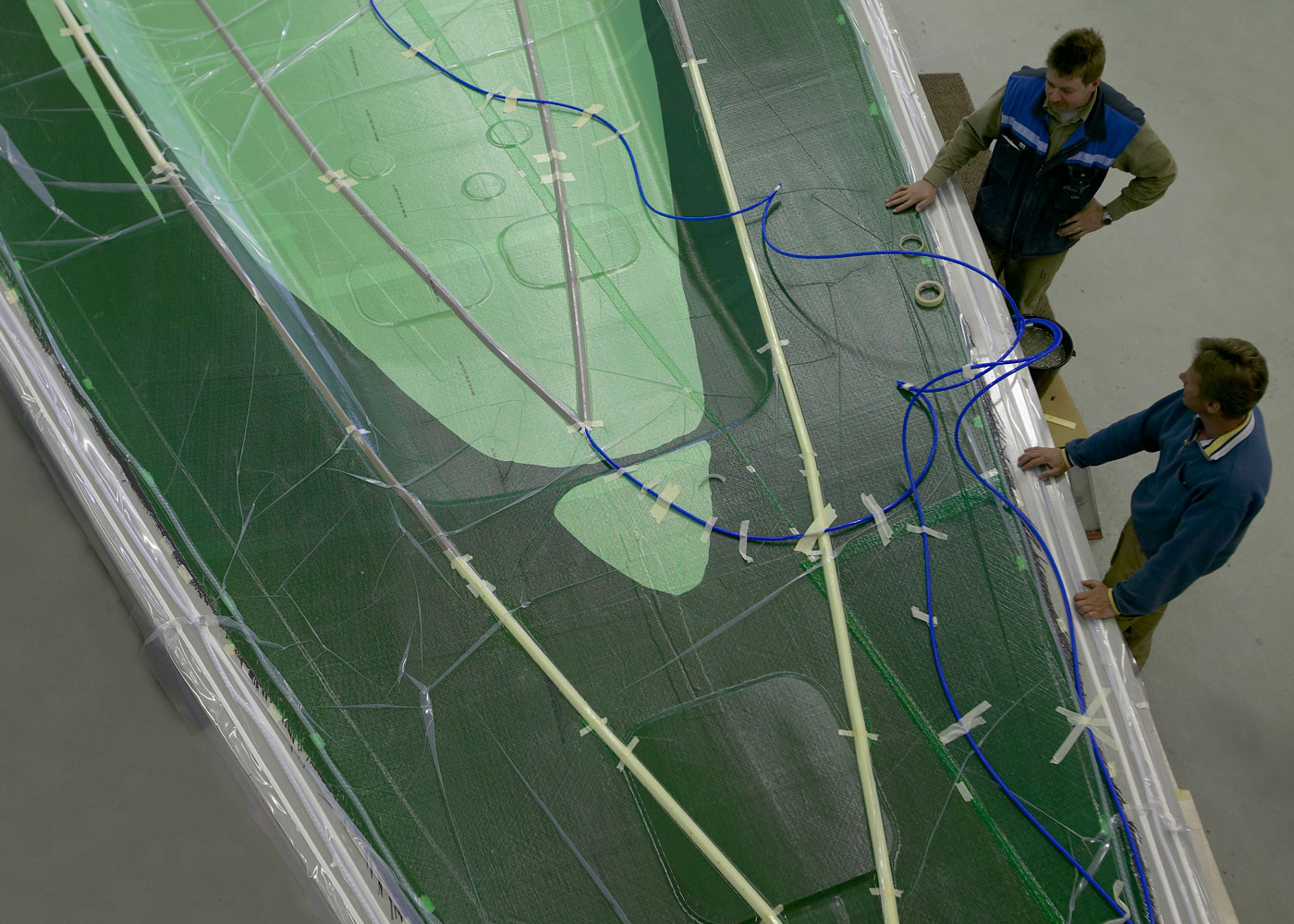
Deck infusion under way.
More and more the pre-preg laminates came into used. Pre-preg laminates are fibers impregnated with epoxy. It is done in special “machines” achieving a high control on resin-fiber ratio. Projects grew in size and I Guess we repeated “The World’s largest Carbon pre-preg laminate” a few times.

Pre-preg laminate applied to a hull plug.
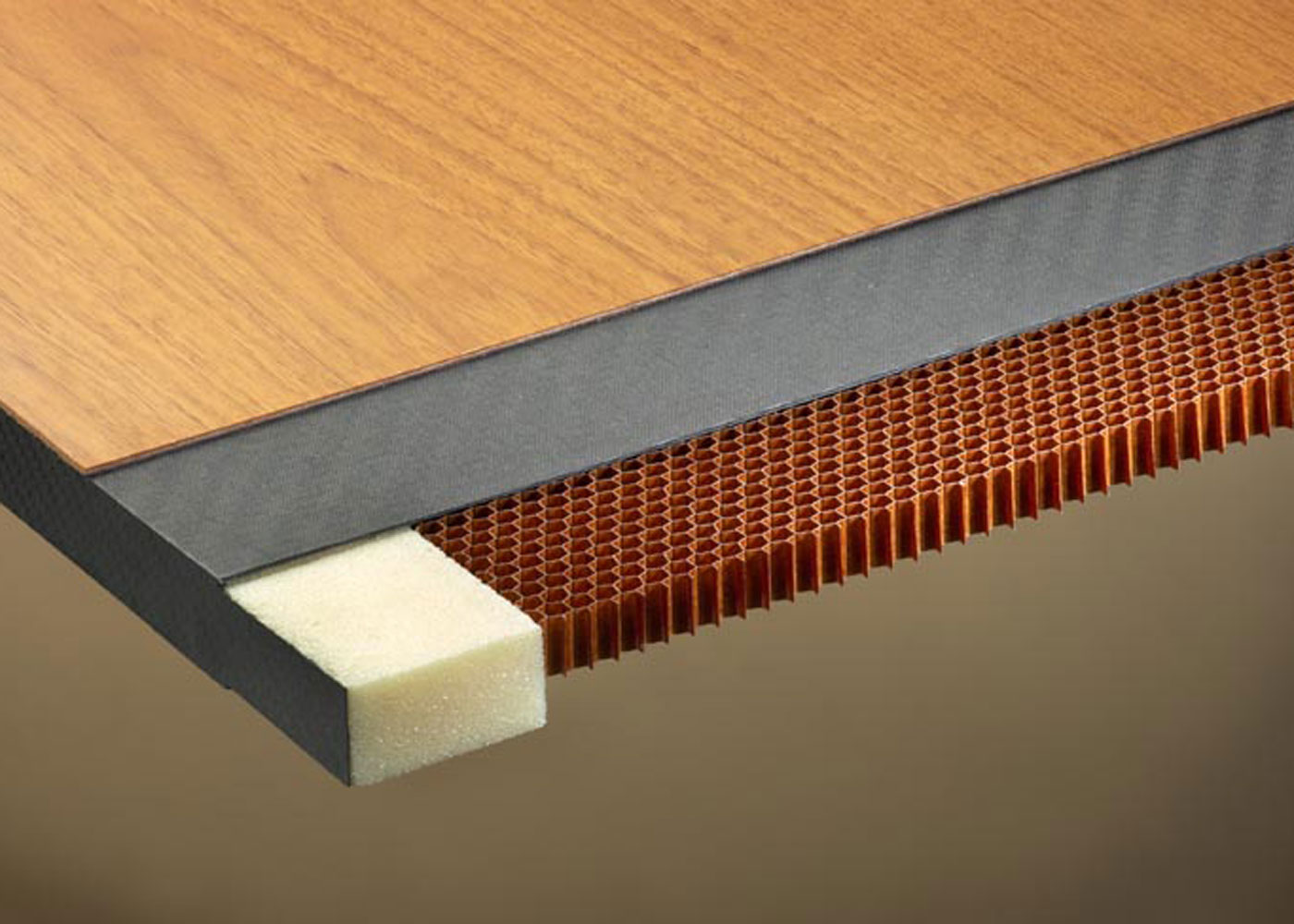
Also, a few different sandwich materials have been used through these years. Starting with End-Grain Balsa and several different density and quality foams and last but not least Nomex honeycomb.
Our original decision to go for a more high-tech way to build boats was based on our strong belief that we could save weight this way, without compromising on safety and quality, on the opposite. We were also convinced that this weigh saving would result in yachts with better performance and sailing characteristics. In the beginning we did get comments from competitors that “they cannot save that much, because even if we take away our total hull weight, we cannot reach these numbers”.
In one way this is true if you only look at hull weight and nothing else but: When working together with Naval Architects, you learn that they have certain main ratios they look at like Ballast/Displacement, Sail Area/Displacement, Length/Displacement etc. and if you for example if you can save 1000 kg in hull weight you can save some in less ballast, if you stay with the same ratio, and with the smaller displacement you need less sail area, less rigg loads both in standing and running rigging, hence less weight and you can do another check on stability, ballast requirement. I used to call this “The mathematical circle of Yacht Design”. The point being that the weight saving is more than what you save in hull weight. How far this “mathematical weight saving” is taken depends on Naval Architect and with the custom project what the client is looking for. In any case the weight saving in, for example the hull, gives the Naval Architect more possibilities to play with. It should also be noted that the hull laminate is only a part of a yachts construction and there are also many other areas where weight can/could be saved without jeopardize strength and quality.
We did have a lot of resistance in the beginning, especially from competitors but also the sailing scene were divided in two groups, the ones that believed that the heavier boat had better performance and the ones that was for the lighter boats. And, in those days, 1973, most of the sailors seemed to support the heavy side.
In order to compete with us, some yards did studies where they claimed that the heavier yacht had better performance. The momentum of the mass pushed their yacht through the waves better than the lighter boat. I got hold of a copy of one competitor’s study where it was also claimed that the heavier boat was faster, and I noticed that in the same study they claimed that, properly done, their compact laminate would even be slightly lighter than Baltic Yachts sandwich construction.
We did not let any of this bother us too much, we were convinced that we were on the right track. We kept doing our work, calculations, and presentations to clients and soon we had clients winning races or just overtaking the neighbors when cruising sailing. Our ideas began to pay off, a good feeling to say the least.
We were, by no mean the only yard promoting sandwich, but we were one of the players.
Looking back and at the same time looking at today’s situation it seems like the competitors that acted against sandwich construction either has disappeared or adapted high-tech sandwich construction which, in my book, is an indication that we did some things right. I am grateful that we managed to stick to our ideas and original philosophy, it paid off.
I am also forever grateful to the clients that had enough fait in us and gave us the opportunity to prove ourselves, without them we would not have succeeded.
1973 and 2021 are two different worlds when it comes to laminating. Probably because almost 50 years has passed.
Although Baltic Yachts laminates year 2021 is extremely high tech I am proud to say that the technology we adapted and developed 1973 are still very competitive in quality and strength in today’s yachting world.
TELL TALES
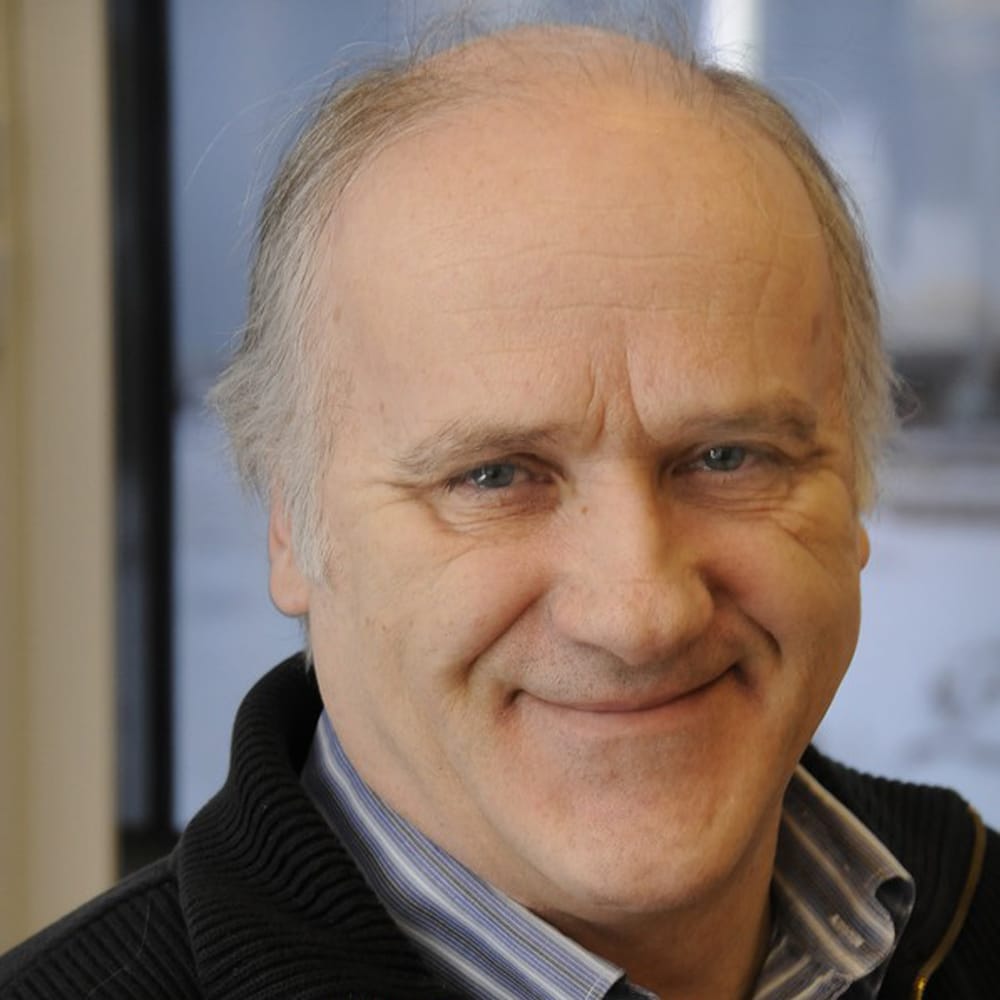
PG JOHANSSON
There can be few yacht builders like PG Johansson, who can boast an unbroken career with the company he co-founded almost 50 years ago. In that time PG Johansson has witnessed every twist and turn of a colourful, exciting and technically pioneering industry accumulating a wealth of fascinating stories, some familiar, some still untold. In this blog PG will be recalling his experiences of the yachts he has built, the people he has met and some of the more unusual events on the journey to turning clients’ dreams into reality.
Would you like to comment on this post or share your own Baltic story? Join our ‘Baltic Yachts Tell Tales’ facebook group exclusive to the Baltic Family.